Metal fabrication is essential to large industries, small businesses, entrepreneurs, and...
Kryton Metals Blog
What is Metal Tooling?
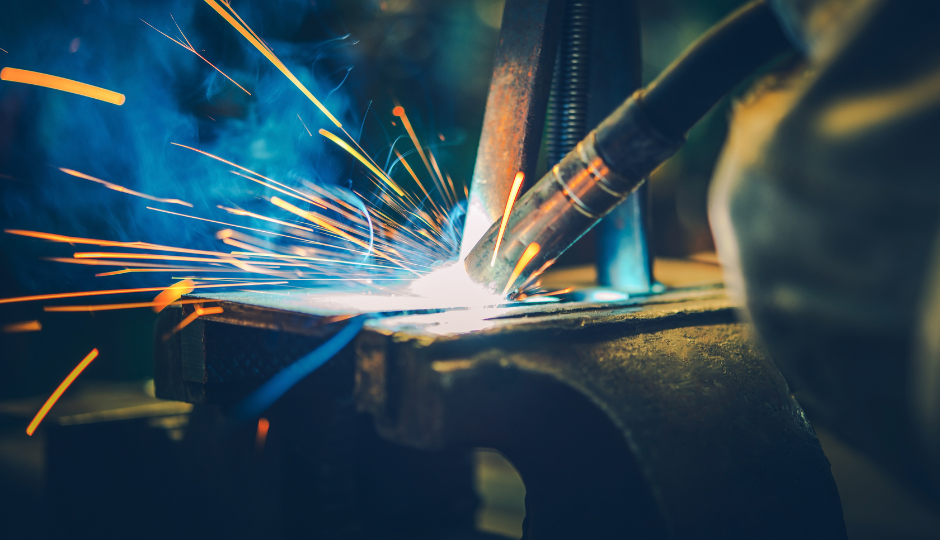
Metal tooling supports innovation for multiple industries, including some that might surprise you. It is a crucial manufacturing process that individuals and organizations have used for centuries. Precision metal fabrication allows companies to develop groundbreaking products from sheet metal. Experts can use customized metal tooling techniques to tailor designs around complex geometries and strict manufacturing standards. This article will explore the importance of metal tooling in various industries. We will introduce sheet metal tooling as a process, explain its significance, and examine its applications.
What Is Metal Tooling?
Metal tooling is a critical fabrication technique for creating, modifying, and repairing metal parts, components, or assemblies. Experts use specialized metalworking tools and equipment to achieve specific tolerances and innovate efficiently. Manufacturers also may utilize CNC machining for custom metal fabrication projects involving the following:
- Metal spinning
- Metal joining
- Metal cutting
- Metal finishing
- Stamping and forming
In some cases, metal tooling plays a central role in manufacturing. Automated tooling systems are ideal for large-scale projects and mass production, allowing teams to quickly produce parts and prepare for distribution. Many fab shops use computer-aided design as part of the metal tooling process to assist engineers and ensure precision outcomes.
Metal Tooling Techniques & Industrial Applications
What are the metal tooling techniques most commonly used by modern manufacturers, and which applications are best for sheet metal forming and automated tooling systems? Metal tooling encompasses various methods and uses, both in artistic and industrial contexts. Industrial methodologies include repousse, chasing, etching, die cutting, stamping, folding, and forming, and more. These techniques suit ferrous and non-ferrous metals, such as steel, stainless steel, aluminum, copper, and brass.
Let’s zoom in on the standard metal tooling techniques. Note that each metal tooling process requires a different approach and may involve material restrictions.
Repousse
This metal tooling process shapes material by hammering it from the reverse side. It creates raised designs and relief patterns, which are excellent for artistic and industrial applications requiring decorative, ornamental, or customized features.
Chasing
This technique often “chases” repousse. Engineers use it to refine details created during the initial process. Specialized chasing tools are required to finish metal surfaces, create fine textures, and add intricate features to the design.
Etching
This method is a chemical process that selectively removes metal to create unique patterns and designs. Many teams use it to produce electrical pathways for printed circuit boards (PCBs).
Die Cutting
The die-cutting process cuts or shapes metal sheets using a die or press. Manufacturers utilize it to fabricate automotive, agricultural, and electrical components.
Stamping
Stamping is a metal tooling technique used in mass production processes. The most common applications are coin manufacturing, rivet fabrication, nameplate making, and appliance component development.
Folding and Forming
This method for metal tooling bends, folds, and forms metal sheets into desired shapes and custom geometries. Industrial applications for metal folding and forming include construction, aerospace engineering, automotive design, and general metal fabrication.
The Cost-Effective Approach to Metal Tooling
Custom tooling solutions rely on tooling technology advancements and manufacturing innovations. However, even automated tooling systems have limits and unexpected curveballs. Teams should budget for variables and material waste based on the selected machine tooling methods.
The first step is consulting a metal tooling expert and gathering more information about your project parameters. You can also ask for a metal tooling service quote to calculate a budget and determine cost-cutting measures. Discuss sheet metal property variables, tooling techniques, and expectations.
Tooling efficiency is essential regardless of the industry, so cover these five bases for cost-effective solutions:
- Choose steel, stainless steel, copper, aluminum, or other metals for the best results.
- Discover how metal tooling can help achieve manufacturing goals.
- Define objectives before design validation to avoid unnecessary iterations.
- Explore the available tooling technology advancements and manufacturing innovations.
- Prepare for unexpected setbacks by monitoring supply chains.
Metal tooling techniques can adapt to suit various industries and custom metal fabrication projects. Consider the possibilities when choosing materials, comparing methods, and developing your approach.
CNC machining and metal tooling technologies provide reliable parts for multiple industries, including automotive, agricultural, aerospace, and electrical. Teams can use different materials and techniques to customize outcomes to fit the desired application.
The experts at Kryton Engineered Metals can review your opportunities and provide a metal tooling quote. We’ll help you develop cost-effective tactics for fabricating complex geometries or producing the parts, components, and assemblies that keep your company competitive.