Metal tooling supports innovation for multiple industries, including some that might surprise you....
Kryton Metals Blog
Pros and Cons of Different Metal Fabrication Tooling Techniques
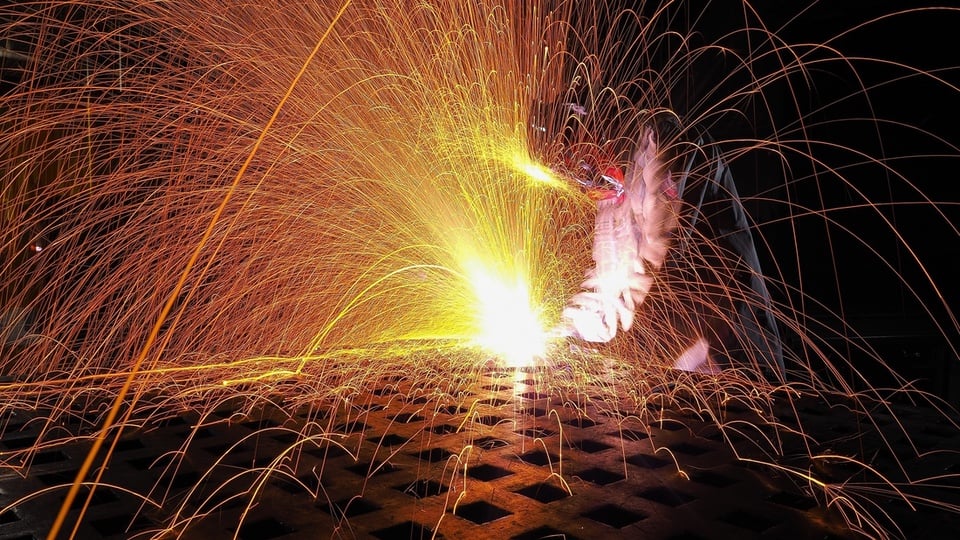
Metal fabrication is essential to large industries, small businesses, entrepreneurs, and individuals. From plumbers and farmers to furniture makers and inventors, the world as we know it would not be the same without engineered metals.
Meanwhile, the metal manufacturing process is complex, which means not all techniques will work for all projects. There are many unique pros and cons associated with rapid tooling sheet metal, including some that may impact your budget. So, here’s what you need to know.
The Top 7 Tooling Techniques in Metal Fabrication
Albeit complicated, metal tooling techniques are relatively flexible in terms of adhering to a customer’s requests. How easily changes can be implemented into a product’s design depends on several factors, including the original blueprints, the software and machinery used, and the skill of each machinist doing the work.
Most CNC machine shops use a variety of different tooling techniques to complete their clients’ complex orders. These common metal manufacturing techniques provide repeatability, dependability, and accuracy across the board.
The top 7 tooling techniques in metal fabrication are:
- Cutting
- Welding
- Punching
- Folding
- Shearing
- Stamping
- Casting
Let’s get into each one a little deeper and talk about what makes them popular.
#1. Cutting
This is a commonly used method that involves separating metal sheets into halves, thirds, quarters, or even smaller pieces. CNC experts can machine both pre-formed workpieces and raw materials to fit a client’s exact specifications.
This is often done using specialized cutting tools such as saws, lasers, or plasma cutters. Cutting is an important step in many metal fabrication projects, as it allows for precise shaping and sizing of the metal, which can then be further processed through bending, welding, and other fabrication techniques.
#2. Welding
Like cutting, welding is another commonly used metal tooling technique. However, it involves joining two workpieces by heating them to a high temperature, causing them to melt and fuse together instead of separating them.
Once the metal cools and solidifies, it forms a permanent, strong joint. Welding is used in many applications, from creating large structures like bridges and buildings, to small household items like appliances and furniture. Machinists therefore use a range of methods and tool types to weld metals for a variety of applications.
#3. Punching
In metal fabrication, punching refers to creating holes or shapes into a metal sheet or workpiece using a punch and a die. The punch is a hard tool that applies force to the metal, while the die is a support structure that helps shape the metal.
The punch is driven into the metal by a press, creating a hole or a cutout in the metal. Punching can be used to create holes for screws, bolts, or other hardware, or to create completely custom shapes in the metal. The process is often used in high-volume production environments because it is fast and efficient.
#4. Folding
Folding is a metal fabrication technique that involves bending sheet metal at various angles to create angled or curved shapes. It's often used to create components for applications like metal enclosures, brackets, and panels.
The process requires specialized machines, such as a press brake, to apply force to the metal and bend it at a specific angle without causing damage to other machined elements or surface abrasion. While folding can be time-consuming, it's a valuable technique that can produce precise, custom shapes that may be difficult to achieve with other methods.
#5. Shearing
Shearing is an efficient manufacturing method used to cut straight lines on long sheets of metal. It is done using a specialized machine called a shear, which uses a sharp blade to slice through the metal. Workpieces may be fed horizontally, vertically, or with an open-edged cutter to trim down the perimeter or create new boundaries for use in larger, more complex components.
It's important to note that while shearing is primarily used to cut straight lines on long sheets of metal, it can also be used to cut other shapes, such as curves or angles, depending on the type of shear used. Additionally, the process of shearing is not always repeated until the designed shape or size is achieved. Instead, the shearing process is typically used as a preliminary step to prepare the metal sheet for further fabrication processes such as bending, stamping, or welding.
#6. Stamping
Stamping is a process that involves cutting or forming a flat sheet of metal into a specific shape using a tool called a stamping press. The metal sheet is placed on the press, and a die is used to cut or form the metal into the desired shape.
The process therefore creates unique shapes, letters, details, and/or images that then get used in several different industries, such as automotive manufacturing, aerospace, and electronics to create a wide range of metal parts and components, including car body parts, aircraft components, and computer parts.
#7. Casting
As one of the oldest types of metal manufacturing, casting is a technique that transforms molten metals into solid shapes using rigid pre-formed molds. The mold is usually made of sand, plaster, or ceramic materials, and it can be designed to create intricate shapes with high accuracy. This method frequently provides an alternative solution to otherwise ineffective fabrication processes.
Casting is used to produce a wide range of metal products, including engine blocks, gearboxes, pipes, and many other components used in the automotive, aerospace, and construction industries. It is also commonly used in art and jewelry making to create intricate and unique designs.
The Pros and Cons of Metal Manufacturing Methods
Metal tooling techniques are often complex, multi-step processes that require experience, intuition, and training. A CNC machining facility can therefore provide the following advantages through efficient metallurgy, although some of the disadvantages cannot be mitigated even with the best experts and equipment on deck.
Advantages
- Precision metal manufacturing renders customized products that suit client and industry requirements.
- Economical metal tooling helps shorten lead times on the production floor and during the prototyping phase.
- Engineers can quickly implement changes to the workpiece design with technical flexibility.
- Products consistently emerge with superior accuracy through CNC programmable software and computerized back gauging.
Disadvantages
- The various techniques used can be extremely labor intensive, which may increase lead times and/or the total tooling cost of each order.
- Odd or unusual shapes, mixed media, and intricate components may require more than one method to complete.
- Some metal fabrication techniques cannot be used in certain industries because of strict production regulations.
Best Metal Fabrication Services for Different Industries
Metal fabrication is a critical aspect of modern manufacturing, and different industries require different techniques to produce high-quality parts and products. For example, the aerospace industry requires components that are lightweight, durable, and able to withstand extreme temperatures and conditions. In contrast, the medical industry requires parts that are sterile and biocompatible. To meet these specific needs, metal fabrication services may offer specialized techniques such as honing, grinding, broaching, milling, spinning, and surface finishing.
Metal engineering plays an integral role in our global economy, but in addition to offering industry-specific services, metal processing companies must also adhere to strict regulations to ensure safety, precision, and consistency. For example, ITAR (International Traffic in Arms Regulations) governs the export and import of defense-related articles and services, while AS9100 and ISO9000 certifications ensure that companies comply with quality management standards.
By adhering to these regulations and standards, metal fabrication services can provide high-quality products that meet the needs of different industries and contribute to the global economy. For more information on how the latest metal fabrication techniques can be used to achieve your production goals, reach out to a KRYTON Engineered Metals expert.