Sheet metal tolerances describe the allowable variations in shape, size, and geometry for sheet...
Kryton Metals Blog
Cost-Effective Tactics for Metal Tooling
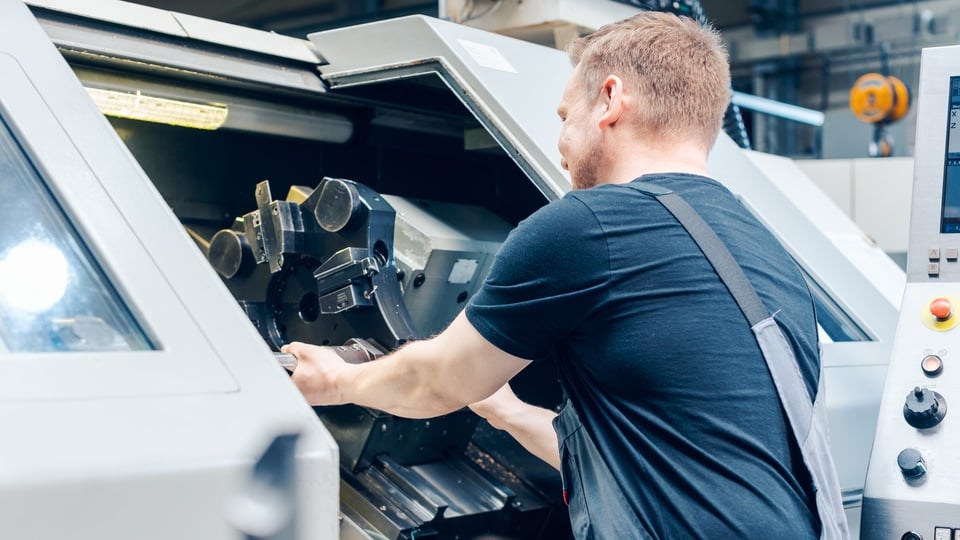
With the rising cost of raw materials, every industry is feeling the pinch. But metal manufacturers face many unique challenges. They must meet the same demands at the same pace while also protecting the profit margin. So, how can they do that without raising prices on the front end?
One solution is to use cost-effective metal tooling tactics. The latest metal market insights point in a concerning direction that predicts even higher costs in the future. That means it’s up to every fab shop to determine and implement the best possible methodologies.
Factors That Affect the Cost of Metal Fabrication
Although sheet metal fabrication is already less expensive than other processes, the cost can still add up. Take, for example, a complex metal part. The more obscure its design, the higher the price to machine it will be.
Furthermore, you might end up prolonging the manufacturing time by accident. If a fab shop isn’t prepared with advanced machines, intelligent software, and state-of-the-art automation, short lead times go out the window.
It also helps a metal manufacturer to possess vast knowledge about materials properties and trending fabrication techniques. However, the total cost of metal tooling usually depends on how many operations a machinist must perform to create each part.
DID YOU KNOW: Metal fabrication shops that have ISO 9001:2015 certification encourage waste reduction, minimize the use of resources, and improve their overall environmental performance, which can indirectly help with reducing raw material costs.
3 Ways to Reduce the Cost of Metal Tooling
For some industries, it may be best to aim for the simplest designs. But for others, the component’s specifications won’t allow as much simplification. So, how do you cut machining costs then? Here are three cost-effective suggestions:
#1. Contemplate the Complexity of Your Design
Special design elements may or may not have a purpose, and that’s something you’ll want to consider. Things like aesthetic embossing, chamfered edges, and blind holes aren’t always necessary for a part to function as intended. They might provide a handsome appearance, but they may also compromise certain industry regulations or reduce safety and functionality.
So, avoid giving too much information to your team but try not to give too little. Meanwhile, practice flexibility with your concepts. Then, communicate specific dimensions and design requirements in your RFQ. And use rapid prototyping (RP) to check the validity of any changes.
#2. Choose the Most Efficient Materials and Finishes
Realistically, you could make the same parts with more easily machinable materials if the design allowed it. An experienced metal fabricator can explain the pros and cons of each alternative option. Plus, choosing a less labor-intensive finish may help cut costs as well.
Popular raw materials such as aluminum and some types of steel are almost always available and easier to machine than other materials, such as stainless steel and titanium—choosing one of these materials may also help you avoid fees for special orders from the shop. Just be sure to consider the processes required to make your part. In some cases, specialty materials may be necessary for safety.
#3. Use Off-the-Shelf Hardware for Simple Metal Parts
If you want an assembly that uses integrated elements to secure certain parts, there may be a cost-effective alternative to fabricating it from scratch. Off-the-shelf hardware can complete some designs while reducing manufacturing costs and decreasing lead times.
Work with your engineer to source prefabricated components. Then, carefully adjust the design to accept those new elements without compromising the functionality—consult with your team to learn more about what off-the-shelf hardware is available and how it can be incorporated into your design.
Reducing the cost of metal tooling can be tricky. So, don’t forget to minimize tight tolerances when you can. Also, try to be mindful of accuracy. Work with a metal fabrication company that understands the unique relationship between material properties and efficient machining.
Cut the Competition with Affordable Metal Manufacturing
Finding the most affordable metal tooling services isn’t always easy, especially not when you have short deadlines and tight budgets to manage. But companies that stay ahead of the curve use expertise to efficiently produce precision parts from quality raw materials. The result: Industries that lead the pack and introduce innovation at a consistent pace.
Reach out to KYRTON Engineered Metals for more information on how to cut metal tooling costs without sacrificing accuracy.