Metal rolling and metal spinning are two distinct fabrication techniques, each using a rotational...
Kryton Metals Blog
Metal Spinning VS Metal Stamping: The Battle to Form and Function
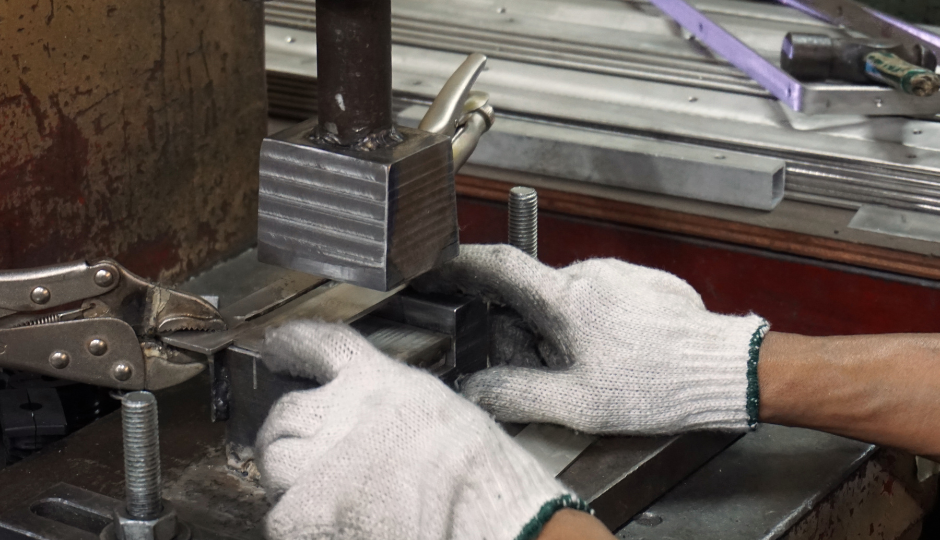
Metal stamping and forming are the foundation of modern manufacturing. This blog will pit two heavyweight contenders against each other in a battle for form and function.
Metal stamping involves precision pressing to create shapes, outlines, and engravings. Metal spinning uses rotational force to form workpieces according to design plans. Both offer unique benefits and drawbacks that we will discuss here. You will learn which technique reins supreme for various applications and objectives.
Let’s delve into metal stamping and forming to determine costs, processes, quality, and efficiency. We will compare and contrast the two metal fabrication techniques to decide the best fit for different projects.
What Is Metal Stamping?
Understanding metal stamping processes is your first step. This metal fabrication method shapes sheet metal into unique forms and functional structures. It involves using stamping presses to apply force, creating different shapes and desired patterns.
Metal stamping processes start with designing a custom metal die. These tools attach to the stamping press, forcefully descending onto the metal to develop a tailored form. The typical applications for metal stamping services include automotive, agricultural, aerospace, and electronics.
Press operators can quickly create complex geometries with precise tolerancing and exceptional durability. Metal stamping is also repeatable, providing consistent manufacturing for a wide range of products used in daily life.
Metal Stamping Pros and Cons
Learn the pros and cons of metal stamping to determine whether or not to use it. Let’s explore and advantages and disadvantages next.
Pros
- High-speed production
- Efficient mass manufacturing
- Excellent precision and design accuracy
- Consistent and uniform results
- Complex geometry creation
- Tight tolerances
- Cost-effectiveness
- Reduced labor waste
- Durable finished products
Many teams prefer metal stamping to metal spinning because it offers value for specific projects. Talk to a metal fabricator for detailed information regarding your goals.
Cons
- High initial setup costs
- Unsuitable for small-scale production and prototyping
- Limited design flexibility
- Incompatible with heavy-gauge metals
- Excess scrap
Teams should consider the trade-offs and limitations when comparing metal stamping and forming.
What Is Metal Spinning?
Understanding metal spinning processes is your next step. Also called spin forming and metal turning, this technique shapes flat metal discs or tubes into symmetrical objects using centrifugal force. Operators begin with a metal blank on a spinning lathe, rotating workpieces at variable speeds to remove surface materials according to geometric specifics.
The plasticity of spun metal allows shaping and stretching without fracturing. Operators can fabricate metal bowls, cylinders, cones, and other custom objects based on specific project parameters. Metal spinning services offer dimensional accuracy and excellent surface finish to eliminate additional operations, cut manufacturing costs, and shorten lead times.
Metal Spinning Pros and Cons
The pros and cons of metal spinning aren’t always apparent. Check out this list to determine if it’s the best process for your project:
Pros
- Exceptional design flexibility
- Symmetrical outcomes
- Geometry versatility
- Suitable for multiple production scales
- Eliminates welding and joining processes
- Reduces assembly expense
- Decreases material waste
Cons
- Limited material options
- Size and thickness constraints
- Tooling complexity concerns
- Processing limitations
- Time-consuming tool fabrication
Discuss the trade-offs when deciding whether to use metal spinning or stamping services.
Metal Stamping and Forming: Use Cases
What are the most common use cases for metal stamping and forming?
- Automotive – Auto parts manufacturers can produce side panels, wheel rims, exhaust systems, fuel tanks, and reflectors with seamless, lightweight, precision fabrication.
- Aerospace – Aviation manufacturers can create engine housings, missile nose cones, fuel tanks, and satellite dish components with high structural integrity.
- Agriculture – Farmers can fabricate custom parts for tractors, irrigation systems, storehouses, and livestock management using a stamping tool or custom metal spinning techniques.
- Industrial – Teams manufacture HVAC equipment, heavy machinery components, pressure vessels, and electrical enclosures for industrial applications.
Other use cases include lighting fixtures, decorations, cookware, utensils, and artistic sculptures. Talk to a metal fabrication expert for more information.
How to Choose Between Metal Forming and Stamping
Make an informed decision. Choose between metal stamping and forming based on multiple factors, including project requirements, part complexity, and desired volume. Also, consider the materials, thickness, tooling costs, and lead times.
Other considerations should include metal tolerancing, surface finish requirements, and secondary operations or post-processing needs. Determine whether your design is simple, complex, or custom to choose the best approach.
Conclusion
The battle between form and function rages on, with metal stamping and forming the two top contenders. Outcomes can vary based on several factors, such as design complexity, materials, and production volume. Compare processes with a metal fabrication expert to develop a comprehensive project plan that aligns with industry standards.
Reach out to Kryton Engineered Metals for guidance in making an informed choice. Ask about project quotes and request information about previous projects to discover the possibilities.