US-fabricated metal parts are essential to our national economy as well as international trade....
Kryton Metals Blog
Precision and Speed: Benefits of Modern Laser Cutting
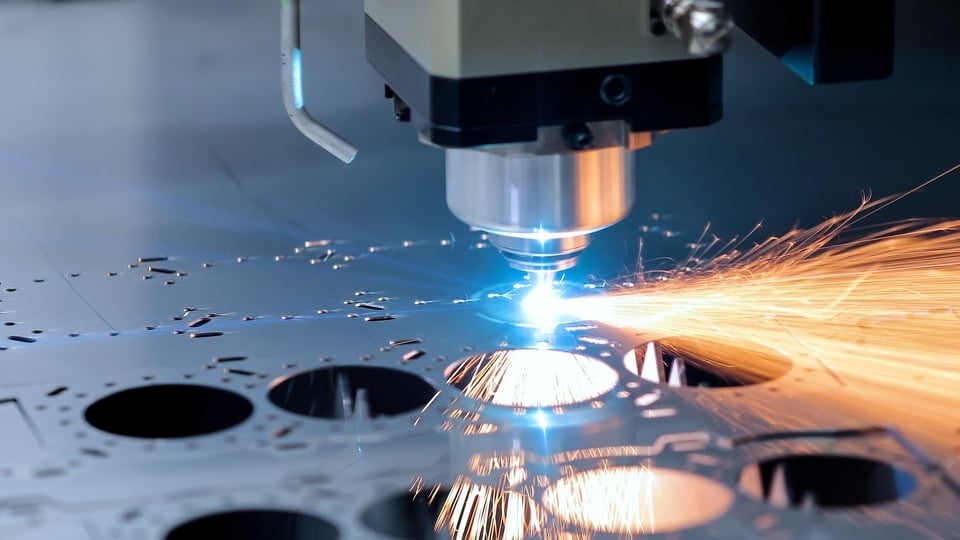
Manufacturers are constantly seeking ways to make their processes more efficient and accurate. Laser cutting has emerged as a solution to many of the challenges of creating specialized metal parts. This article will explore the benefits of modern laser cutting and how it can help manufacturers achieve higher precision and speed.
How Is Laser Cutting Used?
Modern laser cutting delivers superior precision and can create more complex parts than traditional cutting processes. These advanced technologies enable fabricators to produce high-quality parts quicker and more cost-effectively. In the precise world of metal manufacturing, intricate designs are often cut by high-quality laser cutting machines, most of which are operated by expert metal fabricators in line with industry standards.
Manufacturers use laser cutting as the first step of their processes, often meeting or exceeding consumer expectations and serving business partners. Here are some of the most common applications:
- Art: Laser cutting allows artists to create intricate designs and patterns in their work, providing a level of precision hard to achieve by hand.
- Automotive components: Complex parts such as engine components and decorative elements are often produced using laser cutting for exactness and consistency.
- Aerospace parts: High-strength and precision components, vital in the aerospace industry, are regularly made using laser cutting techniques.
- Lighting: Decorative and precise elements in lighting fixtures can be efficiently produced using laser cutting, contributing to both function and aesthetics.
- Furniture: Laser cutting enables the creation of detailed patterns and accurate fittings in furniture manufacturing.
- Agricultural equipment: The production of durable, high-quality parts for agricultural machinery often involves laser cutting.
- Jewelry: Laser cutting enables jewelers to design and produce intricate and finely detailed pieces with precision.
- Interior décor: From decorative panels to intricate fittings, laser cutting plays a significant role in interior décor production.
- Medical utensils: In the medical field, laser cutting is used to create precise and sanitary tools, aiding in complex surgeries and procedures.
- Tools: Laser cutting is employed in the production of a wide variety of tools, ensuring exact dimensions and high-quality finishes.
- Patterns and templates: For accurate replication, laser cutting is often used to create precise patterns and templates in various industries.
- Food products: Even in the food industry, laser cutting is utilized for shaping products or creating food-safe molds and cutters.
Advancements in Laser Cutting Technologies
Modern laser cutters incorporate technologies like computer numerical control (CNC) and automation, offer more versatility in materials and cut with more speed and power. Manufacturers can utilize modern laser-cutting technologies to achieve complex geometries and designs with a high degree of precision and accuracy.
Five-axis laser cutting is another technology in metal fabrication that’s becoming more and more common nowadays with innovative product development. With a big initial investment and a potentially beneficial payoff, five-axis laser cutting is essentially known as 3D laser cutting, allowing operators and manufacturers to cut complex shapes onto pieces that have already undergone metal spinning and forming. The increased speed and precision help teams create standard and non-standard metal parts without sacrificing quality and added costs.
Benefits of Laser Cutting Over Traditional Methods
Modern laser cutting offers high precision, creating intricate designs and complex shapes that traditional methods can’t match. New advancements in laser cutting technology allow for faster and more efficient cuts, reducing production times and increasing throughput. Since modern laser cutting is more of a non-contact process, there’s less wear on tools and reduced risk of material deformation. Overall, laser cutting can be easily automated and repeatable, enhancing consistency and quality across large production runs.
How Manufacturers Are Improving Operations with Laser Cutting
Many manufacturers have reported operational improvements after integrating advanced laser-cutting technologies. The high-profile metal fabricators at NASA, for example, use laser cutters to ensure precise beam positioning in crucial electronics. Other manufacturers use laser-cutting technology to create innovative and sustainable packaging. Laser-cutting technologies help optimize critical processes, enhance existing manufacturing applications, and streamline production. Watch the aerospace, automotive, and agricultural industries for real-time proof, and check out other case studies to see more innovative ways business leaders are employing high-tech laser cutting.
How to Adopt Laser Cutting Technology
Competitive manufacturers understand the importance of adopting and integrating advanced metal fabrication technologies. Those who hold onto traditional processes risk falling behind. Concurrently, the scope of laser cutting applications keeps expanding, accommodating increasingly intricate designs and groundbreaking innovations.
Here are seven tips for joining the laser-cutting revolution:
- Determine your preferred materials. Laser cutting is a versatile process that can be used to cut various materials, such as mild steel, stainless steel, aluminum, non-metals, and special alloys.
- Develop a practical timeline. Laser cutting helps manufacturers satisfy short lead times, but teams need structured plans to ensure accuracy and accountability.
- Create a flexible budget. Unexpected issues do arise, and with supply chain issues, it’s better to be prepared for potential delays or shortages in material availability, leading to additional costs.
- Watch the supply chain. Keep an eye on international trade relations and choose US-made metal to minimize costs.
- Work with an ISO-certified metal fabricator. Develop and manufacture products that adhere to globally recognized standards.
- Adopt laser cutting as soon as possible. Doing so will help you remain relevant in your industry by manufacturing parts with high precision and speed, driving innovation and boosting profitability.
Laser cutting can improve operations and help teams stay ahead in the competitive manufacturing landscape. To learn more, subscribe to the KRYTON Metals blog.