Metal tooling supports innovation for multiple industries, including some that might surprise you....
Kryton Metals Blog
How the Air Movement & Ventilation Industry Relies on Metal Fabrication
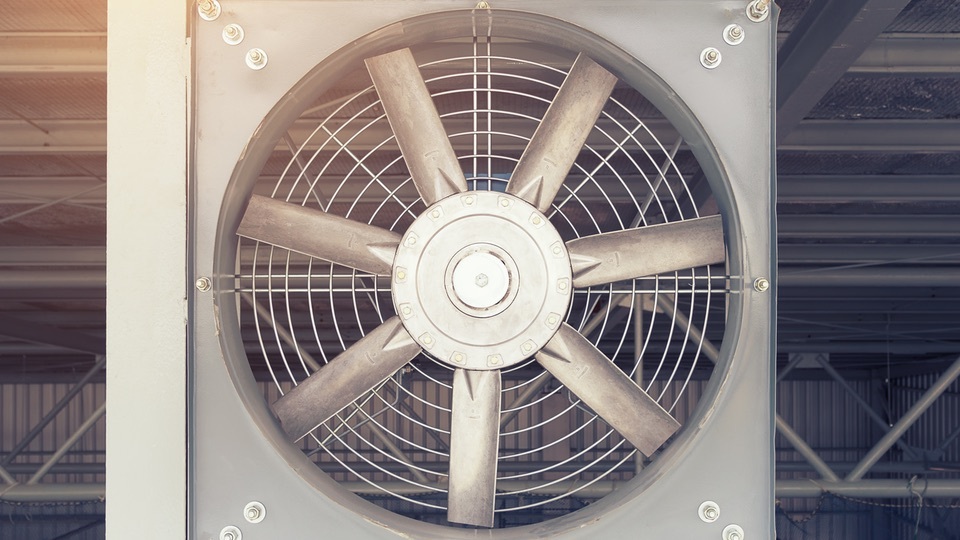
Manufacturers in the air movement and ventilation industry require reliable information and dependable metal fabrication to cater to a diverse clientele. Precision CNC machining services are essential for producing functional ventilation designs and meeting critical demands in this sector.
As ISO standards and consumer expectations continue to evolve, industrial HVAC systems must adhere to metal manufacturing regulations to ensure safety and comfort. In both residential and commercial settings, such as homes or hospitals, efficient air movement is crucial. Inaccurately fabricated metals can compromise the design and potentially endanger occupants.
Here is what you need to know to avoid all that. Plus, we’ll discuss the practical uses of ventilation metal manufacturing, explore the most common fabrication techniques, and review the benefits of CNC machining for the industrial HVAC industry.
Metal Fabrication, Air Movement & Ventilation: Making the Connection
An HVAC system is designed to regulate a structure's heating and cooling adjustments. It consists of various parts, many of which are made of metal. Specific materials aid in maintaining temperatures and protecting system components, making the metal fabricator's role crucial in producing the necessary parts for each system.
Metal fabrication is instrumental in creating components needed for both residential and industrial HVAC system installations. CNC facilities can manufacture a range of components, including exhaust fans, panels, fan domes, and ductwork. Air movement, ventilation, and sheet metal fabrication are closely interconnected. Precision metal manufacturing ensures an airtight fit and consistent insulation, which are vital for passing inspections.
DID YOU KNOW: Precise CNC machining for ventilation components contributes to reduced noise levels and decreased energy waste.
Practical Uses for Ventilation Metal Manufacturing
HVAC companies in the United States generate billions of dollars in revenue annually, catering to a diverse clientele that includes everyday consumers and pioneering developers. To keep up with demand, the industry requires consistent quality and efficient manufacturing processes, making fabrication shops like KRYTON indispensable.
Fabrication experts can create a wide array of air movement and ventilation components using various materials and techniques. Their catalog typically features these sought-after parts:
- Access Doors
- Ceiling Boxes
- Floor Boxes and Registers
- China Caps
- Elbows
- End Caps
- Exhaust Fans
- Damper Sleeves
- Duct Sealants
- Duct Booster Fans
- Flex Ducts
- Flashing
- Fan Panels
- Manifold Gauges
- Hanger Straps
- Reducers
- Return Air Diffusers
- Supply Air Diffusers
- Industrial Fans
- Fan Domes
- Plenums
- Pancake Tapers
- Saddle Taps
- Start Collars
- Straight Boots
- Stackhead Boots
- Vent Caps
- Wyes
For a complete list of the industrial HVAC parts available, reach out to your CNC design team.
Metals and Tooling Techniques Used in Industrial HVACs
A dependable fabrication shop consistently aligns the material and technique to produce functional metal parts for industrial HVAC systems. This is crucial because heat transfer properties can vary depending on the material used, as different materials have varying heat transfer properties. System designs must incorporate components that operate effectively based on their specific applications.
Fortunately, sheet metal fabrication is a relatively well-established process within the air ventilation industry, which has developed standardized practices over time. As a result, HVAC engineers typically utilize similar materials and tooling techniques across various projects.
HVAC Metals List
HVAC metal fabricators use these materials to produce precision ventilation parts at rapid speeds while still obeying ISO standards:
- Aluminum: Lightweight and resistant to rust, aluminum is commonly used in ductwork, grilles, and diffusers due to its excellent heat transfer properties and ease of fabrication.
- Copper: With its superior thermal conductivity, copper is often used for heat exchangers, refrigeration lines, and cooling coils.
- Stainless steel: Another popular material for its corrosion resistance, stainless steel is often used in areas with high humidity or corrosive environments, such as laboratories or hospitals.
- Galvanized steel: Known for its corrosion resistance and durability, galvanized steel is widely used for ductwork and other HVAC components.
By using the appropriate materials, HVAC metal fabricators ensure the durability and efficiency of the systems they create. This attention to detail ultimately results in better performance, increased energy savings, and a more comfortable environment for the end-users.
Ventilation Tooling Techniques
Industrial ventilation and air movement systems rely on precise manufacturing techniques to take full advantage of the materials' properties. These are some of the most common tooling techniques used in HVAC metal fabrication:
- Cutting: This process involves dividing large metal sheets into smaller pieces or customized shapes.
- Prototyping: This stage entails creating tailored components for innovative designs and prototypes.
- Forming: This technique includes folding metals into specific angles.
- Shearing: This method involves cutting long, straight lines in sheet metal to create pieces for assembly
- Punching: This process creates holes in specific locations for both aesthetic and functional purposes.
- Stamping: This method forms divots or indentations in metal parts without piercing through the material.
- Rolling: This technique shapes sheet metal and other materials into rounded or curved components.
- Assembly: This stage involves joining the formed parts through methods such as riveting or welding.
Working with a fabrication shop for sheet metal manufacturing offers benefits such as rapid prototyping, laser cutting services, and micromachining. It also allows for designing innovative components, testing their efficacy, and implementing design changes without hindering the production process.
Four Benefits of Utilizing a Metal Fabricator for Industrial Ventilation
The air movement and ventilation industry benefits significantly from utilizing expert metal fabrication for creating system components. Here are the top four advantages:
#1. Optimized Airflow
High-quality metal fabricators construct components that promote unobstructed airflow. Their designs and precision machining minimize blockages from debris and other potential obstructions.
#2. Consistent Temperature
Regulation Superior metal fabrication contributes to improved control over heat transfer. This results in more stable temperature management within well-sealed HVAC systems.
#3. Extended System Lifespan
The use of premium materials and precise manufacturing techniques ensures enhanced durability, leading to long-term cost savings for businesses and industries.
#4. Compliance with Building Codes
Expertly fabricated HVAC components adhere to ISO manufacturing standards, making them ready for installation immediately after production, and ensuring compliance with building codes.
Develop industrial HVAC systems designed to last with high-quality metal fabrication and top-notch materials. Cut production costs, reduce noise output, and ensure maximum efficiency with the best tooling techniques and a practical approach.
Reach out to a KRYTON team member today.