Welders can complete a variety of metal fabrication orders with consistent precision by applying...
Kryton Metals Blog
4 Custom Metal Fabrication Techniques Manufacturers Should Consider
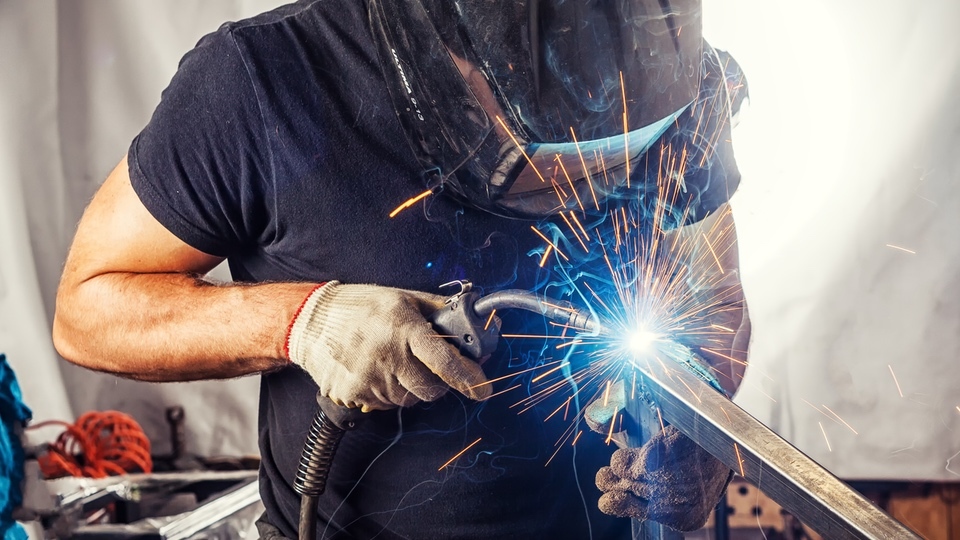
Metal fabrication techniques can vary depending on the desired end product, budget restrictions, and industry standards. There are a wide variety of methods and approaches to consider. Manufacturers can use metal fabrication to create innovative products and complex shapes and then test, finish, and/or distribute based on their goals.
This article will look at custom metal fabrication techniques that manufacturers should consider and discuss common sheet metal fabrication methods to help you make an informed decision. When you make educated metal fabrication choices, you’ll be better able to meet your customers’ needs without sacrificing quality or extending lead times.
Custom Metal Fabrication Techniques to Consider
Advanced metal fabrication uses multiple methodologies with varying lead times, manufacturing requirements, and outcomes. Here are a few to contemplate.
Metal Cutting
Metal manufacturing regularly starts with sheet metal cutting. First, the thickness and material are determined depending on the project’s specifications. Following the design stage, the metal is typically cut using one or more techniques, some of which may be carried out by experts in computerized numerical control (CNC) machining:
Shearing
Sheet metal shearing is a process in which a large cutting tool, known as a shear, is used to cut straight lines on flat metal stock. It delivers clean, straight-edge cuts and is often used to trim down larger sheets to a more manageable size before undergoing other fabrication processes.
Water Jetting
Water jetting, also known as water jet cutting, is a method where high-pressure water, often mixed with an abrasive material, is used to cut through sheet metal. This non-thermal process is precise, versatile, and ideal for cutting heat-sensitive, delicate, or hard materials without distorting the material’s inherent properties.
Laser Cutting
In laser cutting, the operator uses a high-powered laser beam to cut precise shapes in sheet metal. It provides excellent precision, high speed, and the ability to cut complex shapes, requiring expert operation and monitoring for optimal outcomes.
Torching
Torching sheet metal, often through methods like plasma cutting, uses a concentrated flame or plasma jet to cut through the material. This method can handle thicker materials efficiently and is useful for larger, less precise cuts. Usually, fabrication shops tend to avoid torching whenever possible, as it can be tedious with labor and time with high-quantity orders.
Sawing
Sawing sheeting metal is a traditional method where various types of saws, like circular saws or band saws, are used to cut through material. This method is generally used for larger, straight-line cuts and can be effective for both thin and thick metals. Although, this method isn’t generally ideal for repetitiveness.
Metal Bending
Cutting metal doesn’t always make it ready for mass production. Operators might also have to perform other processes, such as bending to form complex shapes. Once the metal is cut, teams can use any of the following metal bending techniques to continue the process:
Form Bending
Form bending is a more general term for bending metal into desired shapes. This process is used to create simple bends and curves in sheet metal. It involves applying pressure at specific points along the metal sheet, often with the use of a die and press, to produce the desired shape. Form bending allows the creation of complex, non-linear bends in sheet metal—it’s frequently used for parts that need curves or angles that aren’t simply straight bends.
Metal Braking
Metal braking, or press braking, involves placing the sheet metal on a flat surface over a shaped die and applying pressure using a punch to create a bend. The press brake applies uniform pressure across the length of the metal, ensuring precise bends. This technique is typically used for creating straight-line bends, such as flanges on a metal box.
Metal Welding
Manufacturing relies on metal welding—a process where two or more pieces of metal are joined together by applying heat, often with the addition of a filler material to form a strong joint. There are also several options within this category, including:
GMAW/MIG Welding
Gas Metal Arc Welding (GMAW), commonly referred to as Metal Inert Gas (MIG) welding, is a versatile process that uses a continuously fed wire electrode and an inert gas, such as argon or helium, to shield the weld from atmospheric contaminants. This technique is favored for its speed and adaptability in joining metals of various types and thicknesses.
TIG Welding
Tungsten inert gas (TIG) welding uses a non-consumable tungsten electrode and an inert gas shield. Fabricators use TIG welding for cutting complex shapes into thick metal sheets. Be aware, however, that the robust cutting tools used in TIG welding could increase your project’s price tag.
Flux-Core Welding
Flux-Core Arc Welding (FCAW) is a variant of MIG welding that uses a special tubular wire filled with flux, eliminating the need for an external shielding gas. The flux provides necessary protection from environmental contamination, making FCAW a good choice for outdoor applications and for welding thicker materials.
SMAW Welding
Shielded Metal Arc Welding (SMAW), often known as stick welding, employs a flux-coated electrode that provides the shielding necessary to safeguard the weld pool. This type of welding is notable for its simplicity and portability, making it a popular choice for construction, maintenance, and repair work.
Laser Beam Welding
Laser Beam Welding (LBW) is a precision process that uses a concentrated beam of light to form a strong, precise weld at high speeds. Frequently used for its capacity to work on small, delicate parts, LBW is also ideal for joining dissimilar or hard-to-weld materials due to its high energy density and control.
Metal Shrinking & Stretching
Metal shrinking and stretching are primarily used to create complex shapes, like curves and contours, in sheet metal parts, such as those found in automotive bodywork, aircraft structures, and custom metal artistry. Here are a few customizable metal shrinking and stretching options:
Heat Shrinking
Heat shrinking involves applying focused heat to a specific area of sheet metal, causing it to contract and effectively “shrink” in size. Experts use this technique in metal forming to remove dents and deformities or to shape curved elements in sheet metal components.
Metal Tucking
Metal tucking involves creating small folds or “tucks” in sheet metal to shrink its surface area. This technique is used to produce complex forms or to correct distortion, especially in custom automotive or aircraft paneling where specific curves or contours are required.
Other Custom Metal Fabrication Techniques
The techniques below can also be used to create unique metal forms:
- Metal stamping—Sheet metal is pressed or punched to create shapes, patterns, designs, and customized indents.
- Die Casting—Molten metal under high pressure is forced into a mold cavity to create complex metal shapes.
- Metal Spinning—Spun metal parts are rotated at high speed and formed on a lathe into an axially symmetric part using a shaping tool.
The metal fabrication experts at KRYTON can help you select the ideal methods for your products, budget, and timeline. Browse our website to learn more about us, or subscribe to our blog for regular updates about metal fabrication techniques and tips.