Manufacturers looking to find a niche in the metal manufacturing industry can explore the...
Kryton Metals Blog
5 Ways Manufacturers Can Take Advantage of Modern Spinning Techniques
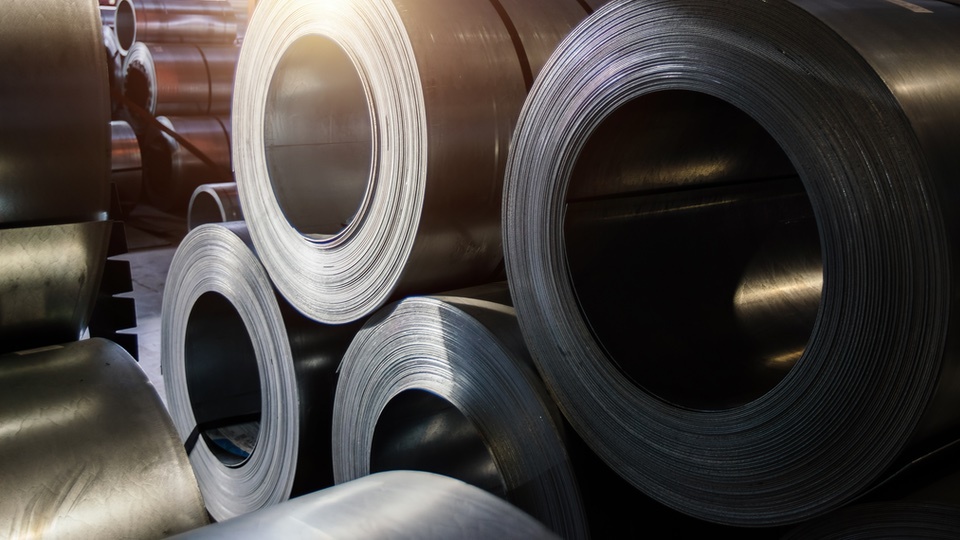
Metal spinning has been a crucial component of manufacturing for centuries. The earliest examples of spun metal exhibited an astonishing level of precision. Over the years, experts have further refined and perfected these techniques. Currently, the metal spinning process operates at high speeds, achieving high production rates and remarkable accuracy.
CNC lathes have become a standard in modern machine shops. Many fabrication facilities offer manual or automated services to produce spun metal. They use advanced machines and robust tooling methods, such as milling or turning, to remove material from a workpiece based on a specific design. Cutting-edge companies can meet tight tolerances, short deadlines, and unique criteria from a simple drawing.
Meanwhile, other techniques can create symmetrical parts without stripping valuable materials. Metal spinning allows operators to form or deform metal over a pre-designed mandrel. This process requires no heat and can be more cost-effective than other options. We’ve come a long way since the use of rudimentary lathes and standard processing methods.
A Brief History of Spun Metal
The history of metal spinning is fascinating, as it’s one of the oldest ways to form sheet metal. Some scholars believe it originated in ancient Asia as a revered art form. Over time, the excellent craftsmanship made spun metal products highly desirable. Eventually, an entire industry developed to meet the increasing demands.
Fast-forward to the American Revolution, where craftspeople were swamped with custom orders for protective gear, weapons, housewares, and tools. Among them was the renowned Paul Revere, a highly skilled silversmith. Much of his handcrafted metalwork is still displayed in museums today.
Today’s spun metal, while less likely to be handmade, tends to be more durable and features superior precision. Modern metal spinning facilities can also work with more challenging materials than traditional alloys. Many are equipped to handle hardened steel, carbon steel, stainless steel, and even titanium.
DID YOU KNOW: Metal spinning was traditionally used for prototyping and short runs. However, enhanced technologies have made it perfect for high-volume, high-quality orders.
Modern Metal Spinning: An Overview
Modern metal spinning processes, often automated using Computer Numerically Controlled (CNC) machinery, have significantly enhanced precision and efficiency. The finished products are typically ready for inspection or distribution immediately after being formed, streamlining production timelines. This evolved metalworking process can transform a blank into a multitude of shapes without wasting energy, resources, or manpower. These advancements not only ensure exact replication of designs but also promote sustainable practices by minimizing material waste.
Modern metal spinning uses lateral force between rollers and a mandrel to achieve specific shapes and sizes. The roller applies pressure onto the metal blank, which is mounted on the mandrel, gradually forming the material into the desired shape. Today, both the roller and the rotation of the mandrel can be controlled through automation and sophisticated software, providing high precision and repeatability unless the design calls for a manual process.
Manufacturers stand to gain significantly from advancements in metal spinning and the products it creates. These improved processes are notably more resource-efficient, and they maintain, if not surpass, the speed of traditional methods. Furthermore, operators have the ability to refine the final design before production, thanks to rapid prototyping (RP) and comprehensive product development processes.
How to Take Advantage of High-Speed Metal Spinning
High-speed metal spinning benefits product designers, engineers, manufacturers, and production teams. It reduces waste, cuts costs, and renders high-precision parts at rapid speeds. You may not be able to use it for every application, but new technologies have made it more practical, accessible, and affordable.
Here are five clever ways you can take advantage of modern metal spinning techniques:
- Optimize Your Design – Ensure that your design blueprints are accurate and ready for the metal spinning process. Consider having them reviewed by a professional if you have any uncertainties.
- Identify Suitable Components – Select the components that are appropriate for manufacturing using metal spinning. Keep in mind that not all parts or assemblies are suitable for this method.
- Choose High-Quality Materials – Choose materials that best align with your design and the demands of the metal spinning process. Discussing the options with your team can help in making an efficient selection.
- Comply with Industry Standards – Ensure your manufacturing processes meet or exceed all relevant ISO standards, especially in terms of CNC machining and metal fabrication. Make sure to conduct thorough quality inspections before product distribution.
- Collaborate with Your Team – Engage with colleagues, partners, and investors to understand their specific needs or suggestions. Strive to incorporate their feedback and requests into your custom design where feasible.
Take advantage of modern metalworking techniques to make the most of your investment. The technologies continually improve to include new and better approaches. You can achieve an excellent outcome in less time and for less money with rapid metal spinning services.
DID YOU KNOW: Many metal fabricators offer no-cost project estimates to help you plan a budget and predict lead times.
Wrapping Up
Join the metal spinning revolution as experts develop enhanced techniques to render outcomes with better accuracy. Whether hand spinning or using a CNC lathe, you should get excited about the new opportunities to manufacture parts. Maintain your integrity while smoking the competition with an improved methodology that’s sweeping the industry.
Contact a KRYTON Engineered Metals expert to find out how you can take advantage. Ask about our leading metal spinning services to discover why we’re the team to beat.