Manufacturers in the metal fabrication sector are likely familiar with laser cutting machines....
Kryton Metals Blog
How to Choose the Right Type of Laser Cutting for Your Next Project
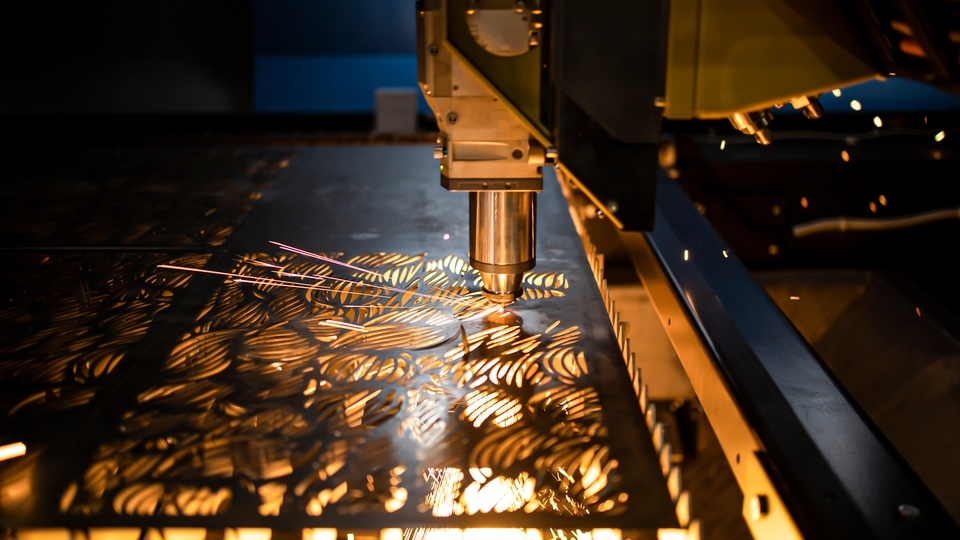
Laser cutting plays a crucial role in the ever-evolving manufacturing industry. As innovative ideas continue to emerge, they necessitate the use of advanced fabrication techniques. For those operating a custom metal manufacturing company, it is vital to have access to top-notch metal laser cutting machines. The question remains: how do you choose the right type of laser cutting for your next project?
Laser Cutting: An Overview
Laser cutting refers to a range of advanced manufacturing processes that utilize high-powered lasers to cut various materials into intricate shapes following a specific blueprint. Modern CNC machine shops often depend on laser cutters to create innovative designs. By employing these processes, it is possible to reduce lead times, lower costs, and achieve exceptional results.
As a result, many competitive manufacturing companies rely on laser cutting services to meet industry demands. Familiarizing oneself with the different types of machines and methodologies can assist project managers in selecting the most appropriate approach.
Laser Cutting Machine Types
Each type of laser cutting machine has its own set of advantages and disadvantages, which may make one more suitable for specific applications than the other. Metal fabrication generally involves at least one of the following laser-cutting machine types:
#1. CO₂
These machines use a gas laser with carbon dioxide as the medium. CO2 laser cutters are widely used for cutting a variety of materials, including metals, due to their high power and versatility.
Some advantages include:
- Versatility: CO₂ Laser cutters are capable of cutting a wide range of materials, including plastics, wood, textiles, and metals. This makes them a more versatile option for fabrication shops that work with diverse materials.
- Better for thicker materials: CO2 lasers generally perform better when cutting thicker materials, as they can provide a smoother edge finish compared to fiber lasers.
Some disadvantages for CO₂ laser cutting machines are:
- Higher operating costs: CO2 laser cutters typically have higher operating costs due to the need for consumable gases, higher energy consumption, and increased maintenance requirements.
- Slower cutting speed: CO2 lasers generally have slower cutting speeds compared to fiber lasers, especially when working with metals.
- Less efficient: CO2 lasers are less energy-efficient than fiber lasers, which can impact long-term operating costs.
#2. Fiber
Fiber lasers utilize a solid-state laser source, offering high precision, efficiency, and speed. They are particularly suitable for cutting metals like stainless steel, aluminum, and brass.
Some advantages to choosing fiber laser cutting are:
- Faster cutting speed: Fiber laser cutting machines offer faster cutting speeds, particularly when working with metals, which can lead to increased productivity.
- Higher energy efficiency: Fiber lasers are more energy-efficient than CO2 lasers, which can result in lower operating costs over time.
- Lower maintenance costs: Fiber laser cutting machines typically require less maintenance, as they do not rely on consumable gases or have as many moving parts as CO2 lasers.
Some disadvantages are:
- Limited material range: Fiber lasers are primarily designed for cutting metals and are less effective at cutting non-metallic materials such as plastics, wood, and textiles.
- Higher initial cost: Fiber laser cutting machines tend to have a higher initial cost compared to CO2 laser cutters.
#3. 3D Laser Cutting (5-Axis)
While it can involve either CO₂ or fiber laser cutting, 5-axis laser cutting is an advanced fabrication technique that allows for precise and intricate cutting in three-dimensional shapes by utilizing a laser that can move along five different axes simultaneously. This cutting method offers greater flexibility and precision compared to traditional 2D laser cutting.
Advantages of 5-axis laser cutting over 2D laser cutting:
- Greater design flexibility: Can cut complex 3D shapes and contours that are impossible with 2D cutting.
- Improved precision: Allows for more precise cuts and finer details in the finished product.
- Reduced need for secondary operations: Can often achieve the desired shape in a single pass, reducing the need for additional machining or manual finishing.
- Less material waste: Optimized cutting paths can lead to reduced material waste and improved efficiency.
Disadvantages of 5-axis laser cutting over 2D laser cutting:
- Higher initial cost: 5-axis laser cutting machines are generally more expensive than 2D laser cutters.
- Increased complexity: The setup and programming of a 5-axis laser cutter can be more complex, requiring additional training and expertise.
- Slower cutting speeds: Due to the intricate nature of 5-axis cutting, cutting speeds may be slower than 2D cutting for some projects.
- Higher maintenance costs: The complexity of the machinery can lead to increased maintenance costs over time.
#4. 2D Laser Cutting
While it can involve either fiber or CO₂ laser cutting, 2D laser cutting is a widely used fabrication method that involves cutting flat sheet materials with a high-powered laser, producing clean and precise cuts along two axes (X and Y). This process is suitable for a variety of industries, including automotive, aerospace, and electronics.
Advantages of 2D laser cutting over 5-axis laser cutting:
- Lower initial cost: 2D laser cutting machines are generally less expensive than 5-axis laser cutters.
- Faster cutting speeds: For flat materials and simpler designs, 2D laser cutting can achieve faster cutting speeds than 5-axis cutting.
- Easier setup and programming: 2D laser cutting is typically less complex, making it easier to set up and program.
- Lower maintenance costs: Due to the simpler machinery, maintenance costs for 2D laser cutters may be lower than those for 5-axis machines.
Disadvantages of 2D laser cutting over 5-axis laser cutting:
- Limited design flexibility: Can only cut flat materials and lacks the ability to create complex 3D shapes and contours.
- Less precision for complex parts: For parts with intricate details or complex geometries, 2D laser cutting may not achieve the same level of precision as 5-axis cutting.
- Potential need for secondary operations: Some projects may require additional machining or manual finishing after 2D laser cutting, adding time and cost to the process.
- Higher material waste: Less optimized cutting paths in 2D cutting may result in increased material waste compared to 5-axis cutting.
KRYTON Engineered Metals offers multiple metal laser cutting services to suit the evolving needs of several industries. Experts can help you choose the best approach for cost-effectiveness and high-quality outcomes. Reach out or request a quote for more information.
How to Choose the Right Laser Cutting for Your Project
Choosing the right laser cutting type for your manufacturing project can be tricky. It’s best to consult a sheet metal fabrication company first because multiple factors can determine the best method. Material properties, lead times, tolerances, and other concerns are essential to getting precise results.
Prepare for a detailed discussion about your project goals and budget objectives. Here is what your team will want to know:
#1. The Material List
Determine the appropriate materials required for your project and identify the most suitable processes for your design. Engineers may need to develop a customized approach for fabricating specific metal parts. While choosing materials like aluminum or stainless steel might offer cost savings, it's important to consider the best option for each unique application.
#2. The Cutting Speed
Your metal fabrication shop should be knowledgeable about the optimal cutting speeds for various metals to achieve the desired results. However, several factors may necessitate adjustments to the process, so be prepared for minor alterations to the initial plan. Additionally, it is not uncommon for a project to require multiple laser cutting techniques to achieve completion.
#3. The Maintenance Costs
When planning the production of metal components, it is essential to consider the cost of various laser cutting services. While it may be tempting to choose more affordable options, compromising on quality may lead to unsatisfactory results. Consult with your team to identify efficient methods that save both time and money without sacrificing the quality of the final product.
Wrapping Up
In conclusion, selecting the right type of laser cutting for your project is crucial for achieving optimal results, cost efficiency, and overall satisfaction. As you navigate the various options available, remember to consider factors such as material type, project complexity, and budget.
By thoroughly evaluating your requirements and collaborating with a skilled team of professionals, you can confidently make an informed decision and bring your project to fruition with the highest quality and precision.
Choose the correct process for your metal fabrication projects and reap the benefits of efficient manufacturing. Contact a KRYTON representative to get started today.