When it comes to metal fabrication, choosing the right material is crucial for the success of a...
Kryton Metals Blog
5 Common Types of Metal Used in Tooling
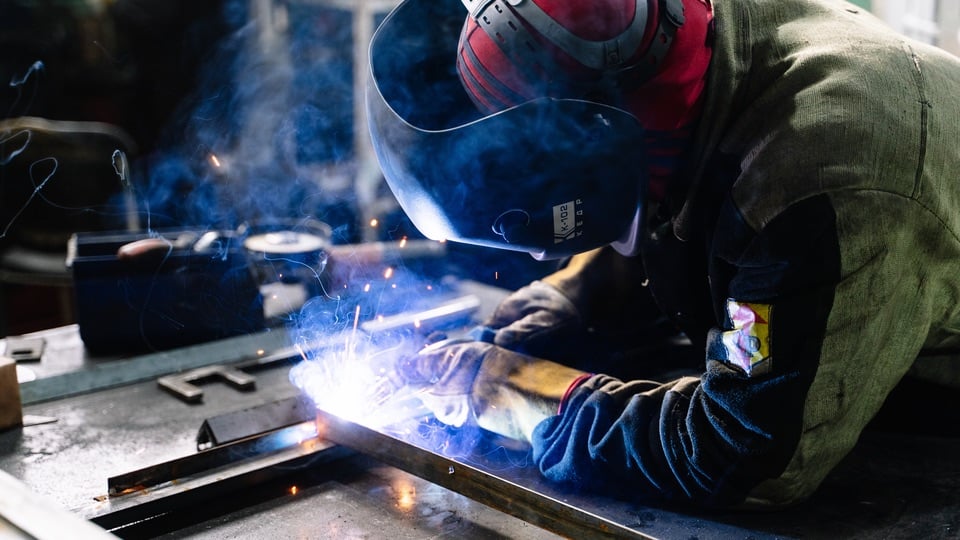
Each fabrication shop has a unique inventory of metal products. And each one uses a different cutting method to make those products. For example, stainless steel manufacturing requires specific tooling techniques to adhere to safety guidelines. Meanwhile, aluminum machining may require something different.
Serious manufacturers depend on high-quality pieces of metals and raw materials for precision tooling. But they also require innovation and flexibility. A little thought leadership can go a long way when it comes to precision CNC machining and metal fabrication. And an innate knowledge of material properties can help shorten lead times and save money.
Why Knowing Common Tooling Materials Matters
Metal fabricators need consistent quality to keep up with industry demands. Reliable information is second only to dependable material sourcing and comprehensive services. However, it can be challenging to find the best fab shops when you’re unsure of the types of metal available.
Furthermore, effective project management means juggling several options to ensure efficiency. That’s because metals can react strangely with different materials. Sometimes, those oddities are beneficial to the bottom line. Other times, they can slow down production or even compromise product quality.
A metal that makes sense for one project may not make sense for another. So, it’s crucial to work with a team of experienced CNC machinists in an advanced metal fabrication shop.
The 5 Most Common Types of Metal Used in Fab Shops
Modern fabrication facilities may or may not use a variety of raw materials. Some specialize while others take a broader approach to manufacturing. Either way, staff should be able to tell you which types of metal are best for your project. Here are five places to start in the meantime:
1. Steel
Steel is undoubtedly one of the most common types of metal used in fabrication shops worldwide. It is a highly versatile metal that can be easily shaped and manipulated to create a vast array of products. Steel's strength, durability, and resistance to corrosion make it an ideal choice for many applications, from construction to manufacturing. Additionally, it is widely available and cost-effective, making it a popular choice for many fabrication projects. The versatility of steel, combined with its strength and affordability, has made it one of the top five most commonly used metals in fabrication shops worldwide.
2. Aluminum
Aluminum is another common type of metal used in fab shops. Prized for being a lightweight, corrosion-resistant, versatile, and durable metal, it can easily be machined and welded. First made in the 19th century, today’s automotive and aerospace industries depend on it. Being relatively inexpensive, it can oxidize and corrode when exposed to salt. So, aluminum may not satisfy some project specifications or industry regulations.
3. Stainless Steel
Stainless steel, widely regarded for its corrosion-resistant properties and durability, is an ideal material for various applications across industries, such as construction, automotive, and aerospace. There are over 3,500 different grades of steel. And the latest estimates put the global demand for stainless steel at nearly two billion tons per year. The United States alone consumes almost 97 million tons of it. But the fact that stainless steel prices are rising may cause concern for some manufacturers. Thus, it may not be the best option despite its favorable properties.
4. Copper
Copper is a common metal found in fabrication shops due to its excellent electrical conductivity, corrosion resistance, and ductility. It is often used in electrical wiring, plumbing systems, and heat exchanges. Copper is also a popular choice for decorative purposes, such as architectural details and ornamental sculptures, due to its unique color and malleability.
5. Brass
Brass, a metal alloy composed primarily of copper and zinc, is commonly found in fabrication shops due to its malleability, corrosion resistance, and attractive gold-like appearance. It is often used for decorative purposes, such as doorknobs, lamps, and musical instruments, as well as for plumbing fittings and electrical components. The versatility of brass makes it a popular choice in various industries, including architecture, automotive, and aerospace.
There are more than just those five metals commonly used in fabrication shops. Other popular metals include titanium, nickel, and zinc, each with their own unique properties and benefits for specific applications.
Top-Quality Tooling Materials and Expert Guidance
In conclusion, understanding the properties and applications of different metals is essential in tooling, where the right material can make all the difference in precision and durability. The five common types of metals used in tooling, including steel, aluminum, stainless steel, brass, and copper, each offer their own set of benefits and drawbacks.
By choosing the right metal for the job, tooling professionals can optimize performance, efficiency, and cost-effectiveness.
This is your chance to be part of the next revolution in metal fabrication. Join forces with an innovative team that can help streamline your projects and determine the most advantageous approach.
KRYTON Engineered Metals houses a vast inventory of high-quality raw materials for metal fabrication. And we also understand how metal properties interact. Come pick our brains for better tooling outcomes.