Laser cutting plays a crucial role in the ever-evolving manufacturing industry. As innovative ideas...
Kryton Metals Blog
3 Things to Know About 5-Axis Laser Cutting
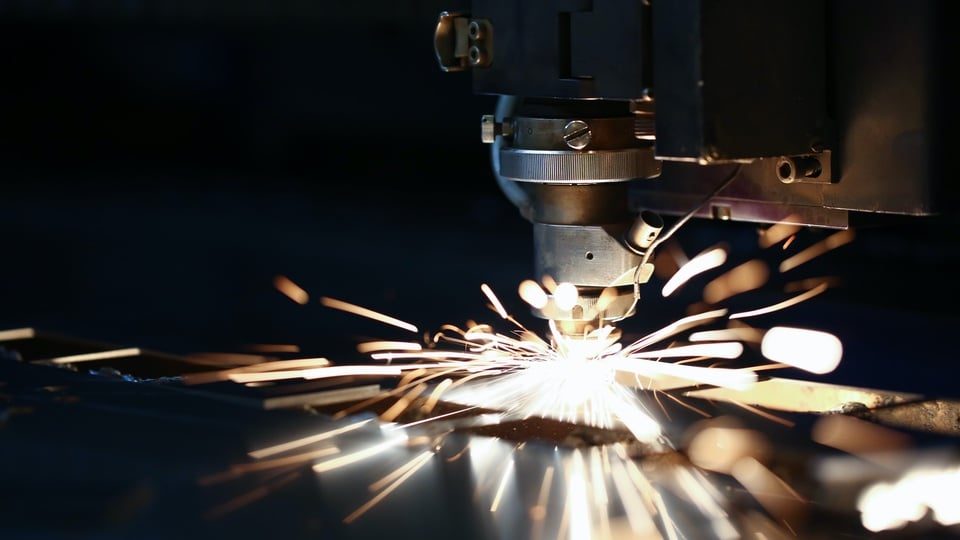
Manufacturers in the metal fabrication sector are likely familiar with laser cutting machines. Laser cutting, which is usually the first step int he fabrication process, involves using a focused laser beam to cut shapes and designs into various materials, such as steel, aluminum, brass, and more. The powerful beam removes material by burning, melting, or vaporizing it.
Until recently, most laser cutting machines only operated along three axes: left and right (X), in and out (Y), and up-and-down movement of the laser cutting head (Z). However, with technological advances in machine tools, 5-axis movement is now available in most modern-day laser cutters. This includes the original X, Y, and Z axes, as well as two additional rotary axes — roll (A) and pitch (B) — allowing the laser beam to approach the part from all directions.
If you are considering having your parts machined on a laser cutter, you must know about:
- The advanced Y-axis cutting within fiber laser cutters.
- Different combinations of gases and materials create laser cuts that vary in quality and speed.
- 5-axes laser cutting provides more advantages over 3-axis cutting.
Let's expand and get into more details with the 3 things you should know about laser cutting machines.
1. Advanced Y-Axis Cutting in Fiber Laser Cutters
The advancement from 3-axis to 5-axis laser cutting has resulted in major gains for the metal fabrication industry. In the traditional two-dimensional cutting, which is most commonly used for flatbed laser work, the Y-axis is rarely involved. This is because the cutting is done on sheets, which makes the Y-axis almost unnecessary.
However, with the advanced movements in 5-axis laser cutting and the addition of two new axes, the Y-axis has been revamped in order to communicate with the other four axes. The advanced movements in 5-axis laser cutting have several other benefits as well, such as increased precision and flexibility.
2. Different Laser Beam Sources Create Different Cuts
According to a study done by the Laser Cutting Machine Market, the sales of laser cutting machines increased at a compound annual growth rate of 2.4% by volume from 2017 to 2021. With the growing demand in these machines, both CO₂ and fiber laser cutters are options.
CO₂ laser cutters use a mixture of carbon dioxide, nitrogen, and helium to create the laser beam, which is guided by a series of mirrors and lenses. Although these machines are somewhat outdated, CO₂ lasers are known for their ability to cut through thick materials accurately, making them a popular choice for most industrial applications.
On the other hand, modern-day fiber laser cutters use a solid-state laser source, which is essentially a long, thin strand of glass and other materials combined with rare-earth elements that creates a high-energy laser beam directed onto the material being cut. Fiber lasers are known for their precision and speed, making them an increasingly popular choice for a wide range of cutting applications.
In summary, both CO₂ and fiber laser cutters are types of machines used for cutting materials such as metal, wood, plastic, and more. The main difference between them lies in how they produce and deliver the laser beam that does the actual cutting.
3. 5-Axis Laser Cutting Has Specific Advantages
The advancement from 3-axis to 5-axis laser cutting has not only expanded the range of shapes and designs that can be cut, but it has also led to other significant improvements in the process.
While 3-axis laser cutting is already a versatile process, 5-axis laser cutting adds some significant advantages:
- More cuts with one setup: Fewer setups mean increased efficiency, more consistency, and less chance of mistakes.
- Adding holes on an angle: The tilting and rotational abilities of 5-axis makes it possible to add holes at different angles without removing and re-positioning the workpiece.
- Improved metal stamp house trimming: Using a 5-axis laser cutter allows hole patterns to be cut out on a finished part, a big improvement over a stamp house. Meanwhile, trimming helps clean the edges of the metal part and relieves pressure on the material.
- Forming the part before cutting: 5-axis laser cutting allows a part to be welded, shaped, and formed before it is cut, resulting in greater accuracy, faster production speeds, and a stronger finished part.
- Cutting complex parts: Perhaps the most significant advantage to 5-axis laser cutting is its ability to machine complex parts that are both high in quality and 100% repeatable.
Consider Your Options Before Choosing a Laser-Cutting Process
Effective laser cutting—whether from a 3-axis or 5-axis machine--typically starts with input from a skilled engineer following best practices. Here are a few points that engineers and operators should remember:
The type of material should determine the laser cutting process: It’s incumbent upon designers and engineers to match the laser cutting process to the material. For example: Wood and certain polymers can be engraved but don’t lend themselves to precise cutting, while nearly any type of laser cutting is effective on most metals.
Increased laser power doesn’t necessarily mean faster cutting: Laser cutters need time to accelerate, making high-wattage lasers effective on large parts without intricate features. On smaller, complex parts, the laser never reaches the high cutting speeds since it is constantly repositioning.
With the proper equipment and metal fabricator, 5-axis laser processing can dramatically improve the quality and result of metal parts. If you’re looking for complex, 3D parts or secondary processing, KRYTON Metals has developed a proven process.
Interested in learning more about current trends in the metal fabrication industry? Check out our full blog.