In the world of construction and engineering, choosing the right metal for projects in harsh...
Kryton Metals Blog
Is Powder Coating the Right Choice for Your Metal Fabrication Project?
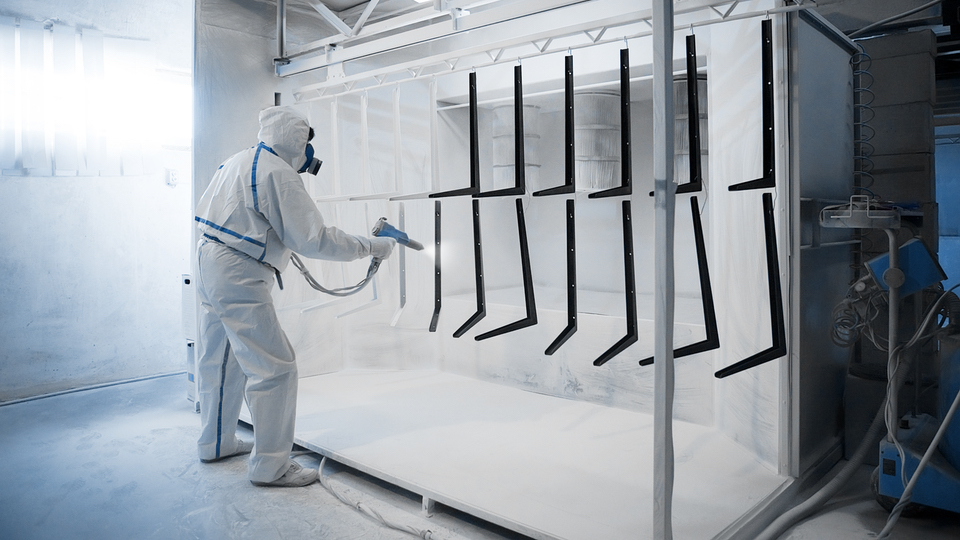
Powder coating is an increasingly popular option for finishing fabricated metal parts and products, offering quality results at cost-efficient prices. As a popular custom metal fabrication finishing option, powder coating is standard on most industrial equipment and suitable for many commercial projects. It uses a high-voltage electrical charge to fuse the dry powder to a variety of sheet metals, providing excellent adhesion and enhanced durability to many raw materials.
Below, we explore several questions to help you determine whether powder coating is the right choice for your project.
How does powder coating work?
Sheet metal is coated with dry powder and then imparted with a positive electric charge to ensure adherence. After the application of the powder, the metal part is then heated, or ‘cured’, in an oven. The heat causes the powder to melt into a uniform film, creating a smooth and durable finish. Depending on the product’s purpose, this can enhance its appearance, functionality, and/or affordability. Powder coating creates a harder finish than traditional paint and provides a broader range of colors for branding and custom design. This manufacturing method is suitable for various metals, including cost-efficient options.
What metals are best for powder coating?
Powder coating creates a durable, tough finish, making it an excellent option for many applications. Below are some of the most common metals treated with powder coating:
- Steel: Both mild steel and stainless steel are commonly powder coated due to their wide usage in manufacturing and their ability to effectively hold the powder coat.
- Aluminum: Aluminum is another popular metal for powder coating due to its lightweight nature and wide usage in various industries like automotive, aerospace, and construction.
- Iron: Both wrought iron and cast iron can be effectively powder coated. This is particularly popular in outdoor furniture and ornamental ironwork.
- Brass: While less common than the other metals listed, brass can also be powder coated, often used in fixtures and decorative elements.
- Copper: Like brass, copper can also be powder coated, although it's rare, due to it being a precious metal.
- Zinc-Coated Metal: Zinc-coated materials, such as galvanized steel, are also suitable for powder coating.
Remember, proper surface preparation is key for successful powder coating application, regardless of the metal being used. Cleaning the surface to remove oil, dirt, rust, or old paint will allow the powder coating to adhere properly and last longer. Some metals are not suitable for powder coating, and it should never be applied over rust or damaged materials. Talk to your fabrication team about the best finishing solution for your project.
Are there disadvantages to powder coating?
While powder coating offers many advantages, it may not be ideal for all metal fabrication projects. Certain vibrant colors may fade over time when exposed to direct sunlight, and the application process, which involves special equipment and high temperatures, can present challenges. Particularly thick layers can also be difficult to achieve without surface defects.
How long does powder coating last on metal?
High-quality powder coating applied in metal fabrication typically lasts about 20 years, the lifespan can vary depending on the specific processes used and the conditions of exposure. Unlike surfaces treated with conventional paint, powder-coated metals can maintain their integrity even under high temperatures and significant environmental exposure. Most powders are highly resistant to weathering, corrosion, and harsh industrial chemicals, contributing to their durability.
What metals cannot be powder coated?
While many metals are good candidates for powder coating, certain ones don’t lend themselves well to this process. For instance, very soft or porous metals, like lead and tin, are not typically powder-coated as they might not withstand the heat used in the curing process. Similarly, precious metals like gold, silver, or copper are rarely powder coated as it would mask their intrinsic aesthetic appeal. Lastly, metals that have a high level of oxidation or rust may not be ideal for powder coating as the surface imperfections can affect the finish.
Is powder coating less expensive than paint?
While powder coating metals involve higher initial costs, they can reduce overall costs in the long run by supporting short lead times, tight budgets, and high-quality standards. Powder coating can help protect metal parts and create a smooth, even appearance.
Reach out to an industry expert to get more information on whether powder coating is the right choice for your design and discuss the pros and cons of this process. KRYTON has more than 40 years of experience fabricating metal parts. Learn more about our proven process, or subscribe to our blog for more insider tips.