When it comes to metal fabrication, choosing the right material is crucial for the success of a...
Kryton Metals Blog
8 Most Common Materials for Sheet Metal Fabrication
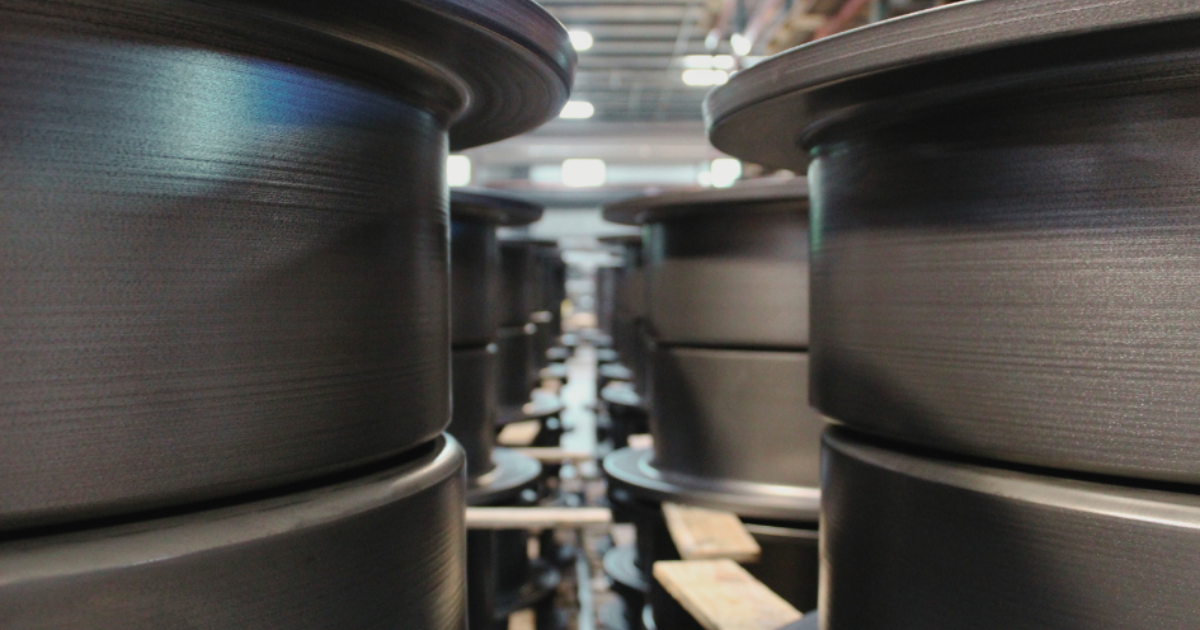
Choosing the right sheet metal can be the game-changer for your project. Whether you're working on a small DIY project or a massive industrial job, understanding the properties of different sheet metals can help you make an informed decision.
Let’s dive into the 8 most common sheet metals you’ll find in metal fabrication shops, exploring their unique advantages, disadvantages, and typical applications.
ALUMINUM
Aluminum advantages:
- Lightweight: Great for applications where weight reduction is key, such as in automotive and aerospace industries.
- Corrosion-Resistant: Naturally forms a protective oxide layer, perfect for outdoor and marine environments.
- Good Thermal Conductivity: Can quickly transfer heat from one place to another, ideal for heat exchangers and cooking utensils.
- Non-Sparking: Ideal of environments with flammable materials, enhancing safety in the oil and gas industries.
- Reflectivity: Can be used as a reflective insulator, improving energy efficiency in lighting fixtures and thermal insulation.
- Recyclability: Highly recyclable and promotes sustainability—most of the aluminum ever produced is still in use.
- Ductility and Malleability: Easily bent and formed, perfect for complex shapes in architectural features and electronics.
- Anodizing Capability: Can be anodized for enhanced corrosion resistance, wear resistance, and vibrant colors.
- Non-Magnetic: Makes it suitable for minimizing magnetic interference in electronic components
Aluminum disadvantages:
- Welding Challenges: Due to high thermal conductivity and oxide layer—requires specialized welding techniques and equipment.
- Low Melting Point: Susceptible to melting or deforming under high temperatures, limiting its use in high-heat applications.
- Thermal Expansion: High thermal expansion can cause issues with structural integrity and fitting in precise applications.
- Galvanic Corrosion: Can corrode quickly when in contact with certain metals, requiring careful material pairing.
- Work Hardening: Can harden and become brittle when worked excessively, complicating complex forming processes.
- Surface Scratching: Soft surface is prone to scratches and dents, requiring additional coatings or treatments for durability.
- Cost Variability: Price fluctuations can be significant, impacting budgeting for large-scale or high-quantity projects.
- Lower Strength: Lower tensile strength compared to steel—have to use thicker sheets or additional support in structural applications.
Industries & Applications: Automotive parts, aircraft components, heat exchangers, and marine equipment.
STAINLESS STEEL
Stainless steel advantages:
- Corrosion-Resistant: Contains chromium, preventing rust and corrosion, making it ideal for kitchen equipment and medical instruments.
- Strength and Durability: Excellent for structural applications and heavy-duty environments, such as marine and industrial.
- Hygienic: Easy to clean and maintain, preventing bacterial growth, which is crucial in healthcare and food industries.
- Self-Healing Properties: Forms a protective oxide layer that self-repairs when damaged, maintaining corrosion resistance.
- Non-Reactive Surface: Resistant to acids, alkalis, and other chemicals, making it ideal for food processing and medical applications.
- Aesthetics: Offers a sleek, modern look with various finishes, including brushed, mirrored, and matte, suitable for decorative purposes.
- Fire and Heat Resistance: Maintains strength and integrity at high temperatures, making it suitable for applications involving heat exposure.
- Sustainability: Fully recyclable with a high scrap value, contributing to eco-friendly practices and sustainability.
- Low Maintenance: Requires minimal maintenance compared to other metals, reducing long-term costs.
Stainless steel disadvantages:
- Cost: More expensive than other sheet metals, affecting budgeting for projects requiring large quantities.
- Work Hardening: Can become harder and more brittle when worked excessively, complicated processes.
- Thermal Conductivity: Poor thermal conductivity compared to other metals, limiting its use in heat exchangers.
- Fabrication Challenges: Difficult to weld, requiring specialized equipment and techniques, increasing fabrication costs.
- Scratching and Dents: Prone to scratches and dents despite its hardness, affecting its appearance and requiring protective coatings.
- Weight: Heavier than other metals, which impacts transport and handling costs as well as structural load considerations.
- Stress Corrosion Cracking: Susceptible to stress corrosion cracking in certain environments, such as chloride-rich conditions.
- Magnetic Properties: Certain grades are magnetic, which may cause electronic interference.
Industries & Applications: Kitchen appliances, medical devices, construction, and food processing equipment.
MILD STEEL
Mild steel advantages:
- Excellent Weldability: Making it easier to join pieces together without compromising strength due to low carbon content.
- Ductility and Malleability: Allowing for easy shaping, bending, and forming into complex shapes without cracking.
- Recyclability: Fully recyclable, contributing to environmental sustainability and reducing waste in production processes.
- Cost-Effectiveness: Relatively low cost compared to other metals, offering a cost-effective solution for various applications.
- Surface Treatment Compatibility: Easily accepts surface treatments like galvanizing, painting, or powder coating, enhancing corrosion resistance and aesthetic appeal.
- Versatility: Suitable for a wide range of applications, from structural components to decorative items, due to its versatility and adaptability.
- High Impact Resistance: Making it ideal for applications requiring durability and toughness.
Mild steel disadvantages:
- Corrosion Susceptibility: Prone to rust and corrosion when exposed to moisture or harsh environments without protective coatings.
- Lower Tensile Strength: Lower tensile strength compared to other steels, limiting its use in applications requiring high strength and load-bearing capacity.
- Thermal Conductivity: Higher thermal conductivity can lead to rapid heat loss or gain, which may not be ideal for temperature-sensitive applications.
- Surface Hardness: Relatively soft surface that can be prone to scratches, dents, and wear, requiring additional treatments for increased hardness.
- Fatigue Resistance: Lower fatigue resistance compared to alloy steels, which can be a limitation in applications involving cyclic loading or stress.
- Weight: Heavier than aluminum, which can increase transportation and handling costs as well as impact structural design considerations.
- Magnetic Properties: While sometimes an advantage, it can be a disadvantage in applications requiring non-magnetic materials, such as certain electronic or medical devices.
Industries & Applications: Construction, automotive frames, pipelines, and general fabrication.
COPPER
Copper advantages:
- Antimicrobial Properties: Has natural antimicrobial properties, making it ideal for applications in healthcare and food processing industries.
- Electrical Conductivity: Exceptionally high electrical conductivity, making it a preferred choice for electrical and electronic components, wiring, and circuit boards.
- Thermal Conductivity: Allows for efficient heat dissipation, which is useful in heat exchangers, radiators, and cooling systems.
- Corrosion Resistance: Due to the formation of a protective patina layer, highly resistant to corrosion in various environments, including marine and industrial.
- Malleability and Ductility: Extremely malleable and ductile, allowing for easy forming, bending, and drawing into intricate shapes and designs without cracking.
- Aesthetic Appeal: Attractive reddish-gold color that develops a beautiful patina over time, adding aesthetic value to architectural and decorative applications.
- Noise Reduction: Effective at dampening vibrations and reducing noise, making it useful in building construction and automotive industries for soundproofing.
- Non-Magnetic: Makes it suitable for applications where magnetic interference needs to be minimized, such as in medical equipment and precision instruments.
Copper disadvantages:
- Cost: Higher cost compared to many other metals, which can be a limiting factor for budget-sensitive projects.
- Weight: Heavier than aluminum and some other metals, which can increase transportation and installation costs, as well as structural load considerations.
- Work Hardening: Prone to work hardening, which means it can become brittle and difficult to work with after repeated bending or forming.
- Thermal Expansion: Higher coefficient of thermal expansion can lead to dimensional changes with temperature fluctuations.
- Tarnishing: Susceptible to tarnishing and oxidation, which can affect its appearance over time and require regular maintenance to retain its aesthetic appeal.
- Galvanic Corrosion: Can cause galvanic corrosion when in contact with certain other metals, such as aluminum and steel.
- Softness: Relatively soft compared to other metals, making it more prone to dents, scratches, and deformation under mechanical stress.
Industries & Applications: Electrical components, plumbing, roofing, and decorative arts.
GALVANIZED STEEL
Galvanized steel advantages:
- Enhanced Paint Adhesion: Surface provides a rough surface that improves paint adhesion, great for painted applications without the need for extensive surface preparation.
- Self-Healing Properties: Zinc coating has self-healing properties—small scratches and damages can self-repair by forming a protective layer of zinc oxide, which extends the life of the material.
- Sacrificial Protection: Zinc coating corrodes in place of the underlying steel upon damage, providing extra longevity even in harsh environments.
- Improved Durability in Concrete: Performs well in concrete, making it suitable for reinforced concrete structures due to its ability to resist corrosion when embedded.
- Cost-Effective Longevity: Durability and low maintenance requirements make it cost-effective in the long term.
- Wide Temperature Range: Can withstand a wide range of temperatures without significant changes in performance, making it versatile for various climates and industrial applications.
- Ease of Inspection: The uniform and bright finish makes it easier to visually inspect for quality control and detect any areas that may require attention.
- Environmentally Friendly: Recyclable and the galvanizing process has a relatively low environmental impact compared to other corrosion protection methods.
Galvanized steel disadvantages:
- Embrittlement Risk: Prolonged exposure to high temperatures can lead to zinc embrittlement, reducing the material's ductility and making it more prone to cracking.
- Weldability Issues: Welding onto zinc coating produces toxic fumes and requires additional ventilation and protective measures. Special welding techniques or removal of the coating may be needed.
- Surface Imperfections: The galvanizing process can sometimes result in surface imperfections such as spangles or uneven coatings.
- Reduced Electrical Conductivity: The zinc coating reduces the electrical conductivity of the steel, which can be a disadvantage in applications requiring high conductivity.
- Galvanic Corrosion with Certain Metals: Can cause galvanic corrosion when in direct contact with metals like copper and aluminum.
- Zinc Runoff Concerns: In outdoor applications, zinc runoff can occur, which may impact the surrounding environment, particularly in aquatic ecosystems—runoff can also stain nearby surfaces.
Industries & Applications: Construction, automotive, HVAC systems, and agricultural equipment.
BRASS
Brass advantages:
- Natural Antimicrobial Properties: Makes brass ideal for applications where hygiene is crucial, such as in medical settings, kitchens, and public spaces.
- Acoustic Properties: Often used in musical instruments due to its excellent acoustic properties, producing a rich and resonant sound that is not easily replicated by other metals.
- Aesthetic Versatility: Can be polished to a high sheen or left to develop a patina over time, providing versatile aesthetic options for designers and architects.
- Non-Sparking Characteristics: Does not spark when struck, making it a safe choice for use in environments with flammable gasses or liquids, such as in fittings used in the gasoline industry.
- Low Friction Coefficient: Low friction coefficient makes it suitable for applications involving moving parts, such as in bearings and gears, reducing wear and tear and extending component life.
- Easy Machinability: Relatively easy to machine and form, making it cost-effective for complex parts and reducing manufacturing time and costs.
- Good Electrical Conductivity: While not as conductive as copper, brass still offers good electrical conductivity, making it useful for electrical components and connectors.
- Resistance to Saltwater Corrosion: Brass exhibits excellent resistance to corrosion, especially in saltwater environments, making it ideal for marine applications.
Brass disadvantages:
- Susceptibility to Dezincification: Zinc in brass may be leached from the alloy, especially in plumbing applications with high chloride content, leading to weakened structural integrity and porous surfaces.
- Stress Corrosion Cracking: Prone to stress corrosion cracking, especially when under tensile stress in corrosive environments, which can compromise the material’s reliability in certain applications.
- Price Volatility: The cost of brass can be more volatile compared to other metals due to its copper and zinc content, affecting budget predictability for large projects.
- Tarnishing: Brass is prone to tarnishing and requires regular maintenance to maintain its appearance, which can be labor-intensive and costly for aesthetic applications.
- Density and Weight: Denser and heavier than many other sheet metals, which can be a drawback in applications where weight is a critical factor, such as in aerospace or automotive industries.
- Lower Strength Compared to Steel: While brass offers good durability, it generally has lower tensile strength compared to steel, limiting its use in high-stress structural applications.
- Limited High-Temperature Applications: Brass has a relatively low melting point compared to other metals, which restricts its use in high-temperature applications and environments.
- Lead Content in Some Alloys: Some brass alloys contain lead to improve machinability.
Industries & Applications: Musical instruments, plumbing fittings, and decorative hardware.
TITANIUM
Titanium advantages:
- Biocompatibility: Highly biocompatible, meaning it is non-toxic and not rejected by the body. This makes it ideal for medical implants and devices, such as joint replacements and dental implants.
- Excellent Fatigue Resistance: Titanium can withstand repeated loading and unloading cycles without failure—crucial for aerospace and automotive components that undergo constant stress.
- Superior Strength-to-Weight Ratio: One of the best strength-to-weight ratios of any metal, making it perfect where both strength and weight are critical, such as in aircraft structures and sports equipment.
- Resistance to Chlorine and Chlorides: Highly resistant to chlorine and chloride solutions, perfect for chemical processing/desalination plants and other places with exposure to these corrosive elements.
- Non-Magnetic Properties: Advantageous in applications requiring non-magnetic materials, such as in MRI machines and certain electronic devices.
- Low Thermal Expansion: Titanium does not expand or contract significantly with temperature changes—beneficial in high-precision engineering applications.
- Long Service Life: Due to its corrosion resistance and durability, titanium parts often have a longer service life compared to those made from other metals, reducing the need for frequent replacements.
- High Melting Point: Titanium's high melting point makes it suitable for use in high-temperature applications, such as in jet engines and power plant components.
Titanium disadvantages:
- High Cost: Significantly more expensive than other metals due to the complexity of its extraction and processing.
- Difficult to Machine: Extremely difficult to machine due to its hardness and tendency to gall and seize on cutting tools—increases machining time and costs and requires special equipment and techniques.
- Susceptibility to Hydrogen Embrittlement: Titanium can absorb hydrogen, leading to hydrogen embrittlement, which reduces its ductility and toughness, causing it to crack under stress.
- Limited Availability: Not as widely available as other metals, which can lead to supply chain challenges and longer lead times for projects requiring titanium components.
- Reactive at High Temperatures: At elevated temperatures, titanium can react with oxygen, nitrogen, and hydrogen, forming brittle compounds that can compromise its mechanical properties.
- Electrical Conductivity: Titanium has relatively poor electrical conductivity compared to other metals, such as copper and aluminum, limiting its use in electrical applications.
- Thermal Conductivity: Titanium has lower thermal conductivity than many other metals, which can be a disadvantage in applications requiring efficient heat transfer, such as in heat exchangers.
- Weight: While titanium is lighter than steel, it is still denser than aluminum, which can be a con in applications where minimum weight is critical, such as aerospace and automotive parts.
Industries & Applications: Aerospace, medical devices, marine equipment, and sporting goods.
BRONZE
Bronze advantages:
- Antimicrobial Properties: Has natural antimicrobial properties, making it suitable for use in environments where hygiene is critical, such as in hospitals, kitchens, and public spaces.
- Low Friction: Makes it ideal for use in applications where reducing friction is crucial, such as in bearings, bushings, and gears.
- Self-Lubricating: Many bronze alloys exhibit self-lubricating properties due to their ability to form a lubricating oxide layer, reducing the need for additional lubrication in moving parts.
- Resistance to Saltwater Corrosion: Highly resistant to corrosion in saltwater environments, making it a popular choice for marine applications, such as ship fittings, propellers, and underwater fasteners.
- Good Conductivity: Good electrical and thermal conductivity, making it useful in electrical connectors, heat exchangers, and other applications requiring efficient energy transfer.
- Aesthetic Appeal: Develops a unique and attractive patina over time, which enhances its visual appeal for decorative items, architectural features, and artistic sculptures.
- High Wear Resistance: Highly resistant to wear and abrasion, making it suitable for use in applications where components are subject to continuous friction and mechanical stress.
- Ductility and Malleability: Both ductile and malleable, allowing it to be easily formed into various shapes and sizes, which is beneficial for intricate designs and complex fabrications.
Bronze disadvantages:
- Cost: Generally more expensive than other common metals like steel and aluminum, which can be a limiting factor for budget-sensitive projects.
- Weight: Relatively dense and heavy, which can be a disadvantage in applications where weight reduction is critical, such as in aerospace and automotive industries.
- Work Hardening: Can work-harden, becoming brittle and more difficult to work with after being subjected to mechanical stress or deformation.
- Oxidation in Air and Maintenance: Oxidation can also lead to the formation of a greenish patina that forms on bronze surfaces—may require periodic cleaning or maintenance.
- Limited Availability of Alloys: Certain specialized bronze alloys may have limited availability, leading to potential supply chain challenges and longer lead times for procurement.
- Compatibility with Other Metals: Can cause galvanic corrosion when in contact with certain other metals, which can be problematic in mixed-metal assemblies.
- Thermal Expansion: Has a relatively high coefficient of thermal expansion, which can cause issues in applications with tight tolerances and varying temperature conditions.
Industries & Applications: Marine hardware, bearings, bushings, and sculptures.
WRAPPING UP
Choosing the right sheet metal for your project can significantly impact its success. Understanding the unique properties, advantages, and disadvantages of each type can help you make an informed decision. Whether you need lightweight aluminum, durable stainless steel, or corrosion-resistant galvanized steel, each metal has its place in various industries and applications.
Ready to get started on your next metal fabrication project? Contact us today to discuss your needs and find the perfect sheet metal for your application. Our team of experts is here to help you every step of the way.