Sheet metal tolerances describe the allowable variations in shape, size, and geometry for sheet...
Kryton Metals Blog
How the Medical Industry Benefits from Metal Fabrication
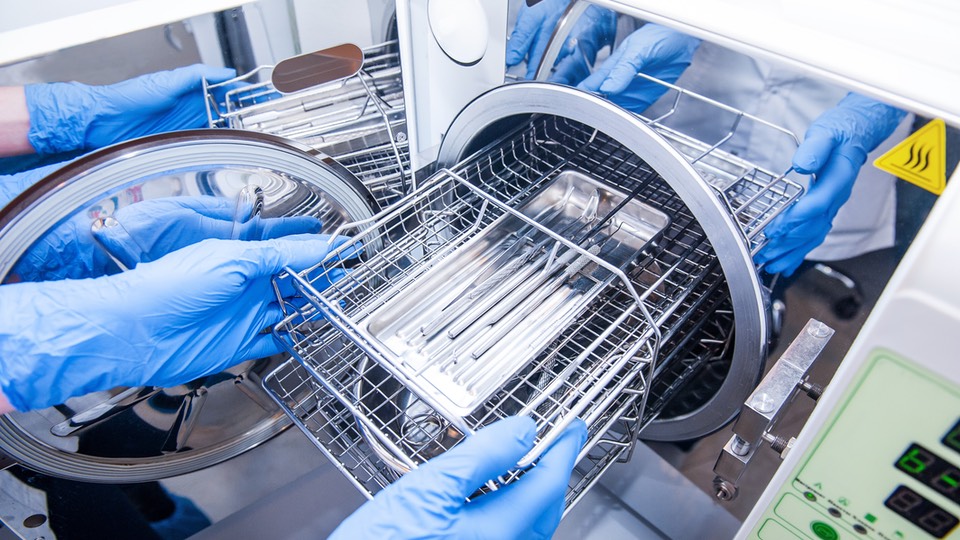
Medical metal fabrication is essential for the healthcare industry. High-quality, custom-made tools and equipment, such as surgical instruments and durable medical carts, are necessary for medical professionals to provide effective and safe care. Nurses, doctors, and surgeons rely on these precision-crafted tools for routine appointments and critical care, ensuring that patient needs are met with the utmost attention and expertise.
The medical industry greatly benefits from custom metal fabrication, but to fully understand its advantages, we should explore typical use cases, common metal types, and custom sheet metal fabrication capabilities. This examination will help illustrate the strong connection between engineered metals and various aspects of medical care, including emergency medicine.
The Top Five Metal Fabrication Benefits for the Medical Industry
Medical devices play a crucial role in saving lives, and the healthcare industry relies on cost-effective equipment to maintain a safe environment. Doctor's offices, clinics, and hospitals require efficient HVAC systems to ensure optimal air quality and temperature control, as well as precision-engineered medical instruments to perform vital procedures effectively.
But that’s only where the benefits of medical metal fabrication begin. Here are five more advantages to explore:
#1. Bespoke Medical Device Production
Engineered metals are fundamental to modern medical equipment. Custom metal fabrication enables the creation of tailored tools designed for specific situations. Advanced fabrication shops can cater to various needs, producing unique products or mass-manufactured inventories. As a result, custom sheet metal fabrication helps medical professionals achieve exceptional performance in their work.
FACT: Medical experts can develop ultra-sensitive sensors and design precisely calibrated tools.
#2. Compatibility with Other Medical Instruments
Sheet metal fabrication enables the production of high-quality, consistent medical equipment. Fab shops can employ ISO-certified techniques to bend, shape, and form stainless steel, aluminum, and other raw materials. Experts with a deep understanding of metal properties utilize laser cutting and metal spinning to achieve tight tolerances. As a result, universities, labs, and hospitals can rely on precision-crafted instruments to support research and provide improved treatment options.
FACT: Generic medical instruments may not be compatible with specific life-saving equipment.
#3. Accurate Parts Made Repeatedly
Enhanced precision and streamlined parts fabrication ensure that the best tools are efficiently delivered to medical professionals. Many medical procedures require reliable accuracy for high-level diagnoses, making it crucial for facilities to provide proper equipment, such as ultrasound machines, MRI systems, and other essentials. Custom metal fabrication plays a vital role in the production of these advanced devices.
FACT: Custom metal fabrication contributes to the development of innovative medical devices, enhancing patient care and treatment outcomes.
#4. Budget-Friendly Enhancements
While providing patients with advanced technologies can be expensive, affordable metal spinning and laser cutting techniques can help healthcare experts innovate more cost-effectively, ultimately benefiting patients. From the initial prototype to the final design, engineered metals contribute to improved healthcare solutions.
FACT: Custom metal fabrication allows for greater flexibility and cost-efficiency in accommodating design modifications during the development process.
#5. Durability Across the Medical Industry
Sheet metal fabrication is an affordable and reliable solution for creating custom medical devices. The resulting products are consistent and durable, often featuring heat and corrosion resistance. Machining experts can produce accurate parts with tight tolerances suitable for various medical disciplines, ultimately enabling medical professionals to perform their duties with greater confidence and precision.
FACT: Many medical instruments require specific designs and metal properties to function correctly.
What Metals Are Used in the Medical Industry?
The most common types of metal used in medical equipment are stainless steel, titanium, and aluminum. However, some medical devices require specialty materials, such as copper, brass, tantalum, and nitinol. It is essential to consult with your team for critical insights, particularly during the design phase.
Titanium is a vital metal for the healthcare industry due to its biocompatibility, which allows it to connect to bones with a lower risk of rejection and support cardiovascular function when implanted. Titanium parts can be found in a wide range of medical devices, from orthopedic pins to retractors. Stainless steel, another important material in the medical field, is used for various applications, such as metal strips, cryogenic containers, and sophisticated electrical components.
Health experts require materials that can withstand extreme conditions for critical procedures. Consequently, they often opt for one of the following materials:
- Tantalum — A hypoallergenic material used in permanent stents and implants for bone or other hard tissues.
- Copper — An antimicrobial metal commonly employed in wiring and electrical components for diagnostic equipment.
- Nitinol — A nickel-titanium alloy favored for its shape-memory properties, commonly used in expandable stents, implants, and staples.
Talk to an ISO-certified technician for more information on metal properties or how each one benefits the medical industry.
Medical Metal Fabrication at KRYTON
KRYTON Engineered Metals collaborates with the healthcare industry to offer dependable metal fabrication services, precise components, and consistent design quality. We also uphold a culture of commitment from the prototype stage to final production. Contact us for a quote or to initiate your next project, as the future of the medical industry may depend on it.