Sheet metal tolerances describe the allowable variations in shape, size, and geometry for sheet...
Kryton Metals Blog
What to Know About Geometric Dimensioning and Tolerancing (GD&T)
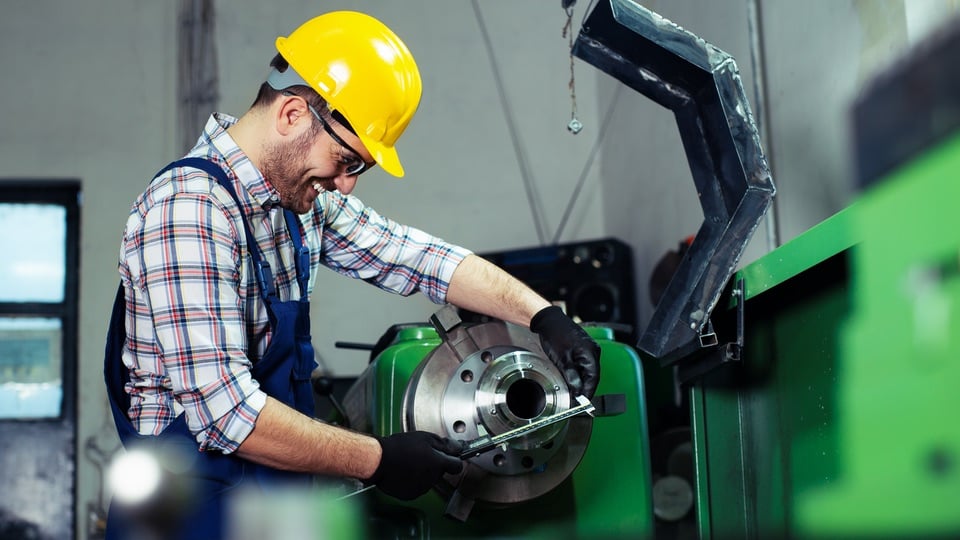
Engineers and machining experts are in charge of managing the many variations in our modern manufacturing process. Meanwhile, fabricated items can differ in size, shape, and dimensions from the initial CAD design simply because of routine machining variables. So, experts often use geometric dimensioning and tolerancing, or GD&T, to communicate and control those variations.
Although it sounds complicated, geometric dimensioning and tolerancing is a relatively simple concept. Basically, it demonstrates the allowable variables within a part’s assembly and then standardizes how each variant gets measured. The most complex aspect is often the code used to program machines, communicate information, and ensure manufacturing consistency.
How Geometric Dimensioning and Tolerancing Works
Blueprints must outline and illustrate the dimensions of all features on a part. Additionally, tolerances for all features on a part must be specified on engineering drawings, along with their acceptable minimum and maximum limits. Since a part’s tolerance is the range of allowable dimensional variation, some engineered drawings can become complicated.
To effectively communicate the designer’s intent, a system of symbols was created. These symbols allow machinists to determine which variations can be tolerated and which cannot. For example, a slightly bent cylinder may not fit into its respective hole due to manufacturing variables. In this case, machinists must control the straightness of the cylinder in a more precise manner than with plus-minus (bilateral) tolerancing.
What GD&T Can and Can’t Do
Before geometric dimensioning and tolerancing was widely used, production was typically limited to strict X-Y axes. As a result, machinists would drill a mounting hole, but that hole had to be within a specific area on the workpiece. This significantly limited innovation and stifled productivity on the machine shop floor.
However, precision tolerancing specifications helped define the same hole’s position within a larger circular area in relation to the intended position. In other words, GD&T ultimately eliminated the innate faults of X-Y tolerancing by reducing the chances of producing a false negative. The process is so efficient, in fact, that it was used during WWII and eventually became the standard for all military manufacturing.
NOTE: The American Society of Mechanical Engineers (ASME) defines Geometric Dimensioning and Tolerancing (GD&T) as a standard which concerns the overall geometry of a manufactured product, as opposed to its surface finish, texture, and/or detailing.
The Advantages of GD&T Implementation
All components must come together seamlessly when fabricating functional assemblies, making complex parts, and creating multi-part products. Relevant features must also be specified in a way that streamlines the production process. Unfortunately, guaranteed precision and functionality are often difficult to promise without a GD&T system in place to give developers and inspectors a chance to optimize the design without busting the budget.
Geometric Dimensions and Tolerancing is also beneficial because it describes the designer’s intentions instead of the actual geometry. Much like a vector formula, wherein the product is merely a representation of the actual object, GD&T helps increase the functionality of a component while shortening production lead times and making it easier to integrate with existing parts.
Put simply, product geometry specifications related to the intended functionality are far simpler than describing those same dimensions in traditional linear notation. GD&T thereby provides a reliable, cost-effective communication tool that serves manufacturers, vendors, quality inspectors, and customers alike.
When performed by an expert, Geometric Dimensioning and Tolerancing even supports statistical process control, or SPC. It may also help decrease parts rejection rates, reduce the need for enhanced quality maintenance, and cut back on assembly failures. In turn, GD&T plays a key role in preserving the essential resources of an organization.
Guidelines for Geometric Dimensioning and Tolerancing
It’s important for engineering drawings to accurately illustrate a product’s design, dimensions, and tolerances without making the project more complex or restricted than it must be. So, machinists and engineers generally adhere to the following guidelines:
- Cut costs by designing for the loosest possible tolerances.
- Move to machine the rest of a part after tolerancing functional features first.
- Angles measuring 90 degrees need not be specified most of the time because they are assumed.
- Most tolerances and dimensions are legitimate at 20 °C / 101.3 kPa.
- Try not to subject dimensions to more than one interpretation.
It’s worth noting that there may be cases where designing for the loosest possible tolerances may not be the most cost-effective approach—it’s also important to consider the specific application and requirements of the product being designed when determining tolerances and dimensions.
Additionally, while most tolerances and dimensions may be legitimate at 20 °C/101.3 kPa, there may be cases where different environmental conditions need to be considered.
Incorporating geometric dimensioning and tolerancing is a wise choice for savvy engineers, but it’s not always a simple process. Reach out to KRYTON Engineered Metals to get more information on how it all works or to talk to an expert about the pros and cons.