Metal spinning plays a significant role in the metalworking industry, although it is not directly...
Kryton Metals Blog
5 Reasons Manufacturers Should Consider Metal Spinning
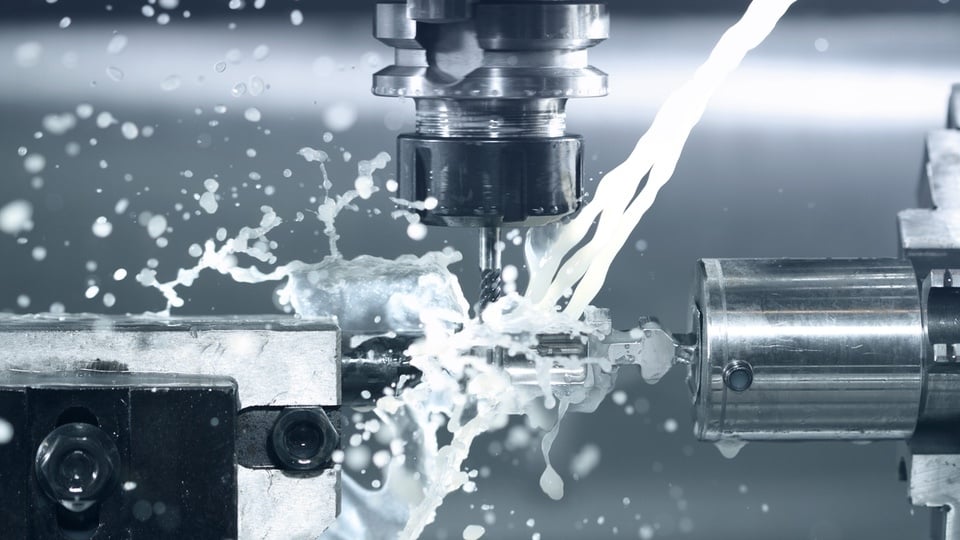
Manufacturers looking to find a niche in the metal manufacturing industry can explore the advantages of metal spinning. This technique has a long history, with fabrication shops employing metal spinning for many years. Today’s modern manufacturing companies can leverage this efficient, fast, and cost-effective process for their benefit.
Manufactured Metal Parts
Product development in metal manufacturing involves multiple stages to create precise metal parts. Prototyping enables engineers to refine designs and explore innovative concepts. As metal spinning techniques continue to evolve, more teams depend on this service to produce prototypes and final assemblies.
Metal spinning involves rotating a workpiece at high speeds to form an axially symmetric component. Fabrication shops can employ either hand-spinning or CNC spinning to achieve accurate results. Each method has its unique advantages and disadvantages, but both can produce metal parts for inspection and application.
Consistently manufactured metal parts are essential for various industries, including agriculture, automotive, aerospace, and infrastructure. These sectors demand practicality and productivity, which metal spinning products can offer. Consequently, numerous industry leaders rely on metal spinning to meet standards and experiment with designs.
Hand-Spinning vs CNC Spinning
Hand-spinning is a traditional method of forming metal parts that requires skilled artisans to operate a lathe and manually shape the workpiece. This technique offers excellent control over the process, allowing for customization and modifications on the fly. However, hand-spinning is more labor-intensive and may not be ideal for large-scale production due to its slower throughput.
CNC spinning, on the other hand, utilizes computer-controlled machinery to automate the metal spinning process. This method delivers high levels of precision and repeatability, making it suitable for mass production of uniform parts. However, CNC spinning can be less flexible in terms of design changes and may require higher initial investments in equipment and programming.
In conclusion, both hand-spinning and CNC spinning have their distinct advantages and drawbacks. Hand-spinning is well-suited for custom projects and small production runs, while CNC spinning is more appropriate for large-scale manufacturing with tight tolerances. Manufacturers should consider their project requirements, production volumes, and desired levels of customization when deciding between these two metal spinning techniques.
The Top 5 Metal Spinning Benefits
Metal spinning is a multifaceted process that incorporates elements of chemistry, physics, computer programming, and other disciplines. Some manufacturers may face challenges when designing products without this technique.
The metal spinning process fosters innovation while maintaining quality, serving as a crucial aspect of contemporary engineering and product development. The numerous advantages it offers are undeniable and essential in today's competitive manufacturing landscape.
Not sure which efficient fabrication method to choose? Here are five practical reasons manufacturers should consider metal spinning services:
#1. Cut Tooling Costs
Metal fabrication can indeed be costly, but metal spinning can be a cost-effective process. By streamlining various processes and delivering high-quality results with consistent precision, metal spinning can significantly reduce manufacturing expenses. Embracing this technique allows manufacturers to optimize their budget without compromising on quality.
#2. Change Designs with Ease
Metal spinning allows for greater flexibility during the design process. Operators can efficiently alter geometries to adjust the intended outcome without generating excessive waste. As a result, manufacturers can save costs by minimizing the need for rapid prototyping and additive manufacturing services.
#3. Shorten Lead Times
By using metal spinning, manufacturers can create a broad array of precision components while adhering to tight schedules and staying competitive. This technique enables faster innovation of concepts and allows companies to introduce new products to the market ahead of their competitors, all while maintaining organizational goals.
#4. Improve Results
Modern metal spinning employs numerous automated functions to produce precise components, and it can also create lightweight parts suitable for a variety of applications. Spun products can be utilized in a wide array of assemblies, enabling testing of new ideas before production or the seamless integration of upgrades.
#5. Tailor Order Volume
Choose between hand-spinning or CNC metal spinning to tailor results for various projects. Utilize consistent methodologies for metal fabrication to ensure design uniformity. Then, determine your order size to calculate an accurate budget and timeline for manufacturing.
Did you know that the standard lead time for metal spinning products is typically three to four weeks? However, in the current market (Q3 2022), lingering supply chain issues can extend this to six to eight weeks. The lead times increase with each additional procedure or operation required. Opting for conventional shear forming or laser cutting could result in higher costs and longer wait times. Consult your team for a detailed timeline and project quote to begin.
FACT: Metal spinning is generally more cost-effective than many other machining or metal fabrication methods.
Wrapping Up
Metal spinning enables teams to create everything from prototypes to final components. It can serve as a practical alternative to rapid prototyping and 3D printing in certain situations. However, product designers must understand the variables to fully leverage the benefits of advanced metal fabrication.
Sophisticated processes are essential for achieving precision and consistency. Regardless of whether hand-spinning or CNC spinning is used, the end results are of utmost importance. Employ metal spinning products to assess designs, test hypotheses, or complete critical assemblies. This approach helps promote productivity and innovation across various industries.
Contact a KRYTON representative today to explore how metal spinning can benefit your project and boost your business’s growth.