In the world of construction and engineering, choosing the right metal for projects in harsh...
Kryton Metals Blog
Galvanized Steel: Different Types, Processes, and Applications
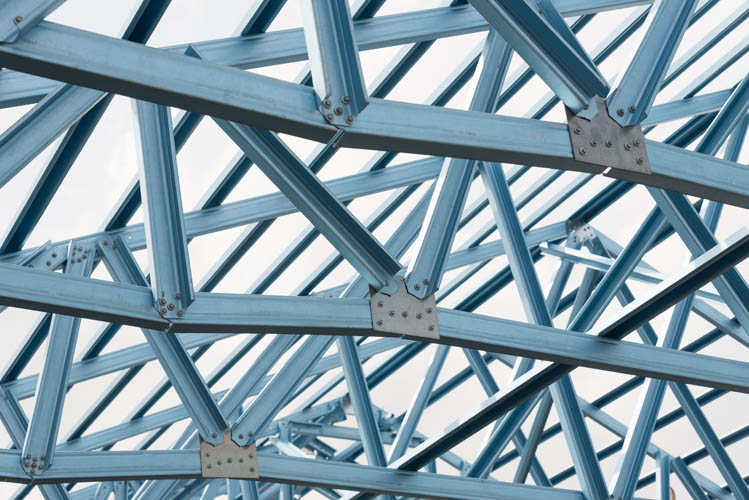
Galvanized steel is a widely used material in various industries, prized for its resistance to
corrosion and red rust through galvanization—a manufacturing process where zinc is coated
to steel to offer protection and prevent rusting. However, not all galvanized steel is created
equal. Different series and grades of galvanized steel offer unique properties and advantages,
making it essential to understand the distinctions when choosing the right material for a
fabrication job or a project.
HOW DOES IT WORK?
There are many galvanizing processes out there, but the most commonly used method is
hot-dip galvanizing, which involves immersing steel in molten zinc. This process initiates a
metallurgic bond between the zinc and the metal. After removal from the bath, the metal
reacts with the oxygen in the atmosphere, forming zinc oxide, which further reacts with
carbon dioxide to create zinc carbonate—this results in a protective coating known as
“spangle.”
APPLICATIONS
Galvanized metals are used almost everywhere from bodies of cars and bicycles to nuts,bolts, tools, and wires. Galvanized steel is also used in:
- Structures - Balconies, verandahs, staircases
- Outdoors - Ladders, walkways, fences, sidings
- Wind/Solar - Solar panel mounting structures, wind turbine towers
- Automotive - Car body panels, chassis and frame components, exhaust systems
- Construction - Highway guardrails, structural framing, roofing and cladding
- Telecommunication - Cell towers, cable support systems, equipment enclosures
- Agricultural - Farm buildings, livestock equipment, irrigation systems
- HVAC - Ductwork/ventilation systems, air handling units, grilles, registers, diffusers
Spinning metal such as galvanized steel is often associated with various industrial
applications. Metal spinners often specialize in shaping galvanized steel and other metals
using precision tools and techniques. Additionally, spin forming and custom metal spinning
services offer bespoke solutions for clients seeking unique designs and specifications.
Metal spinning breathes life into galvanized steel, shaping it to create indispensable
components such as lighting fixtures that illuminate spaces, grain bins that store agricultural
harvests, metal fans that move air, fuel tanks that power vehicles, and an array of other vital
industrial and consumer products.
ADVANTAGES
- Low Initial Cost - In comparison to most treated steels, galvanized steel is more
cost-effective and ready-to-use when delivered, eliminating the need for additional
surface preparation, inspections, or coatings, saving companies time and money. - Longevity - Galvanization ensures that industrial steel can endure for more than 50
years in typical environments, and even over 20 years in severe water conditions,
without the need for maintenance. - Sacrificial Protection - The sacrificial anode makes it so that any compromised steel
remains shielded by the surrounding zinc coating. Even if the steel section is
scratched/damaged and exposed, the zinc will corrode before the steel, providing
sacrificial protection to the damaged areas. - Corrosion/Rust Resistance - While iron elements in steel are highly susceptible to
rusting, the zinc layer serves as a protective barrier, shielding the steel from moisture
and oxygen. This property extends to sharp corners and recesses—areas that are often
challenging to protect with other coatings.
COATING CLASSES
The most common types of galvanized steels out there are G30, G40, G60, and G90, which
have been placed in a zinc bath for improved corrosion resistance for outdoor applications.
The weight of the zinc coating is denoted by the number following the G, such as G90
indicating a zinc coating of 0.9 oz/ft²—if equally applied to both sides of a square foot sheet,
there would be a minimum of 0.45 ounces on each surface.
In most applications and environments, the corrosion performance is directly proportional to
the coating thickness. In other words, G60 has twice the thickness of a G30 coating, and the
life of the product in a given environment is approximately twice as long.
OTHER GALVANIZING PROCESSES
Besides hot-dip galvanization, there are other processes of galvanizing steel. Not as popular
as hot-dip, galvannealing combines annealing and hot-dip galvanizing to create a
specialized, matte-gray finished steel coating.
Akin to hot-dip galvanizing but conducted early in product, pre-galvanizing primes sheet
metal by rolling it through a cleaning agent before immersing it in molten zinc and recoiling
it. This process allows for rapid galvanization of steel sheets on a large scale, ensuring a more
uniform coating.
Distinct from the molten zinc bath, electrogalvanizing employs an electric current in an
electrolyte solution applied to steel, causing zinc ions to deposit onto positively charged steel
surfaces. This process, like pre-galvanizing, is done at the beginning of production and offers
an alternative to traditional methods.
WRAPPING UP
Overall, understanding the differences between galvanized steel processes and types
empowers businesses and manufacturers to make informed decisions based on their specific
needs and requirements. By leveraging the right combination of galvanized steel
components, projects can achieve optimal performance, durability, and cost-effectiveness,
ensuring long-term success and satisfaction.
Want to learn more about galvanized steel or interested in requesting a quote? Click here to
get in touch with us!