In the world of construction and engineering, choosing the right metal for projects in harsh...
Kryton Metals Blog
Aluminum: Different Types, Processes, and Applications
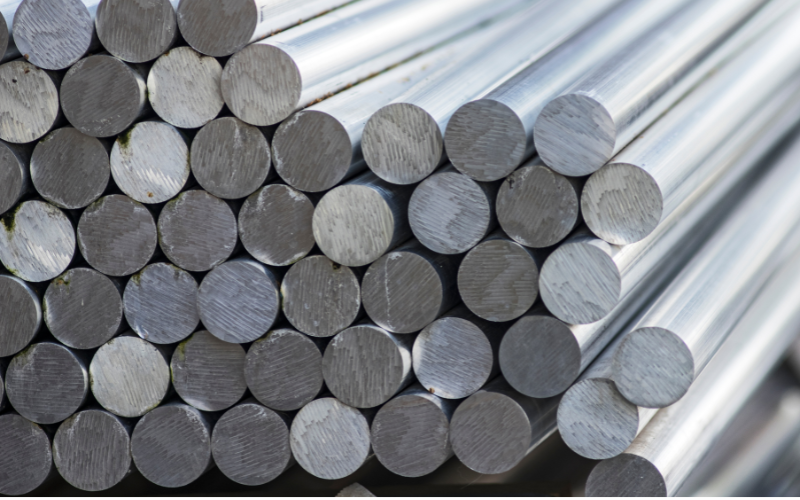
Aluminum, often referred to as the metal of the future, has emerged as a versatile and indispensable material across numerous industries. Its lightweight yet sturdy nature, coupled with its impressive corrosion resistance and recyclability, has positioned it as a key player in modern manufacturing and construction.
However, not all aluminum is created equal. Variations in alloy composition and process techniques yield a spectrum of aluminum grades, each tailored to specific applications and environments. Understanding the differences is critical for selecting the best aluminum alloy to meet the demand of any project.
HOW DOES IT WORK?
Aluminum sheets are manufactured through a detailed process starting with the extraction of bauxite, the primary aluminum source. After refining and smelting, the aluminum is cast into blocks and rolled to achieve the desired thickness. Annealing relieves internal stresses, and finishing processes like cutting and surface treatment ensures that quality standards are met. Precision and advanced technologies are essential for producing defect-free sheets with uniform thickness and mechanical properties.
GRADES
Aluminum has many different alloys, and each alloy is given a four-digit number where the first number indicates the biggest alloying element, the second number (if different from 0) indicates a variation within the alloy, and the third & fourth digit indicate the specific alloy in the series.
1000 Series
The 1000 series of aluminum are essentially known as pure aluminum with a minimum of 99% aluminum content by weight, and it can be work hardened. The most common alloy from this series is 1100 aluminum, which is found in chemical equipment, storage tanks, pressure vessels, protective layers for wires and cables, transformer strips, pots, cooking utensils, automotive engine parts, mufflers, and building decorations.
2000 Series (Copper)
The 2000 series of aluminum are alloyed with copper which can be precipitation hardened to strengths that are comparable to steel. The aluminum-copper alloy can also reduce ductility and corrosion resistance along with the slightly increased susceptibility to cracking which makes some of these alloys difficult to weld. Some uses for the 2000 series of aluminum are aerospace equipment, cryogenics, and aircraft engine cylinders.
3000 Series (Manganese)
The 3000 series of aluminum alloys are typically alloyed with manganese. This series is known for its excellent corrosion resistance and formability, making it suitable for various applications in the automotive, transportation, and construction industries. One of the most common alloys in this series is 3003 aluminum, which is widely used in beverage cans, roofing, and general sheet metal work. The addition of manganese enhances the strength and weldability of these alloys, making them versatile for both structural and decorative purposes.
4000 Series (Silicon)
The 4000 series of aluminum alloys are typically alloyed with silicon. These alloys are known for their exceptional weldability and are often used in welding filler wires and brazing alloys. This series is commonly used in automotive components, bicycle frames, and architectural structures.
5000 Series (Magnesium)
The 5000 series of aluminum alloys are alloyed primarily with magnesium. These alloys are known for their excellent corrosion resistance and high strength, particularly in marine environments. One of the most common alloys in this series is 5052 aluminum, which is widely used in marine applications, such as boat hulls and components, as well as in architectural and structural applications. The addition of magnesium enhances the strength and toughness of the aluminum, making it suitable for various demanding environments.
6000 Series (Magnesium/Silicon)
The 6000 series of aluminum alloys are primarily alloyed with magnesium and silicon. These alloys, like 6061 aluminum, are widely used in structural components, such as extruded shapes, tubing, and profiles, as well as in automotive parts and aerospace components. The addition of magnesium and silicon enhances the overall mechanical properties of the aluminum, allowing it to be easily formed, machined, and welded while maintaining good strength and corrosion resistance.
7000 Series (Zinc)
The 7000 series aluminum alloys, characterized by their high strength, are primarily alloyed with zinc. These alloys are commonly used in aerospace applications, where strength and lightweight properties are critical. They offer exceptional strength-to-weight ratios and are often employed in aircraft structures, such as fuselages and wings, as well as in high-performance sporting goods and automotive components.
8000 Series (Others)
The 8000 series aluminum alloys are relatively uncommon and often experimental, consisting mainly of lithium as the primary alloying element. These alloys offer exceptional strength-to-weight ratios and corrosion resistance, making them potentially valuable in aerospace and automotive industries for lightweight structural components.
Aluminum metal spinning is a widely utilized process in various industries, prized for its versatility and lightweight properties. Aluminum spinning involves forming aluminum sheets or blanks into desired shapes through a spinning process. This method allows for the creation of complex and intricate designs, making it suitable for a wide range of applications in industries such as aerospace, automotive, and lighting.
The aluminum spinning process begins with a blank, typically a flat circular disc of aluminum, which is clamped onto a spinning lathe. As the lathe rotates, specialized tools and dies shape the aluminum blank into the desired form, such as domes, cones, or cylinders. The spinning process can be adjusted to achieve different wall thicknesses and diameters, providing flexibility in design and functionality. Aluminum spun parts are known for their high strength-to-weight ratio, corrosion resistance, and excellent thermal conductivity, making them ideal for components like reflectors, housings, and heat sinks.
TEMPERS
Oftentimes, an aluminum alloy will undergo a tempering treatment—denoted by a dash, followed by a letter, and numbers (i.e. 6061-T6 or 5052-H32). There are four main types of tempers (or letters):
- F: As fabricated
- H: Strain hardened
- O: Annealed
- T: Thermally treated
Several aluminum alloys have a variety of temper designations tailored for specific uses, but some are more common than others. Here is a list of some of the most popular aluminum alloy temper designations, along with their applications:
- 6061-T6: Aircraft fittings, electrical connectors, hinge pins, brake pistons, valve parts, couplings, hydraulic pistons
- 5052-H32: Fuel tanks, appliances, lighting, aircraft fuel lines, rivets, automotive panels, marine components
- 3003-H14: Pressure vessels, food and chemical handling equipment, food packaging, architectural trims
- 7075-T6: Regulating valve parts, gears, bike frames, off-road vehicle sprockets, aircraft fittings, fuse parts
- 1100-H14: Roofing, signage, chemical equipment
WRAPPING UP
Understanding the various alloys and temper designations of aluminum is crucial for businesses and manufacturers to choose the most suitable material for their applications. By selecting the right aluminum alloy and temper, projects can benefit from enhanced performance, durability, and cost-effectiveness. Whether it's for aerospace, automotive, construction, or other industries, making informed decisions about aluminum materials ensures long-term success and satisfaction with the final products.
Want to learn more about aluminum or interested in requesting a quote? Click here to get in touch with us!